記事公開日:2025.06.24
最終更新日:2025.06.27
【製造業向け】スマートファクトリーとは?DX実現の7つのポイント・メリット・導入成功事例をわかりやすく解説
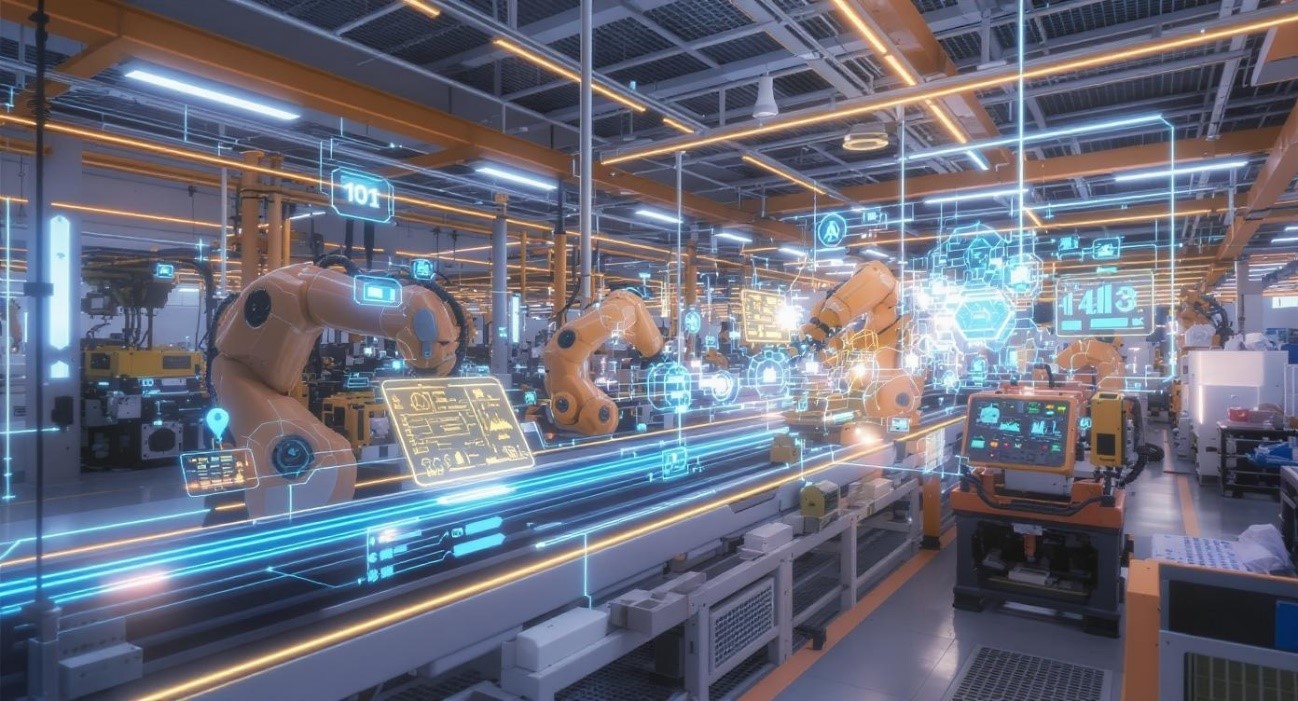
目次
【製造業向け】スマートファクトリーとは?DX実現の7つのポイント・メリット・導入成功事例をわかりやすく解説
近年、製造業界は大きな変革期を迎えています。特にスマートファクトリーという言葉を耳にする機会が多くなっているのではないでしょうか。しかし、「スマートファクトリーとは何なのか」「導入するメリットは何か」「実現にはどのような技術が必要なのか」といった疑問や課題を抱えている方もいらっしゃるかもしれません。
本記事では、製造業のDX推進に不可欠なスマートファクトリーについて、その目的や仕組み、メリット、実現に必要な技術をわかりやすく解説します。さらに、導入における課題と解決のポイント、そして具体的な導入事例を交えながら、スマートファクトリーが製造現場にもたらす生産性向上とものづくりの未来を紹介します。
この記事は、以下のような方々に読んでいただきたい内容です。
- スマートファクトリーの 導入を検討している製造業の経営層や担当者の方
- DXを推進し、工場の生産性を向上させたいと考えている方
- スマートファクトリーのメリットや課題について、網羅的な情報を得たい方
- スマートファクトリーの成功事例から、自社の導入のヒントを得たい方
ぜひ本記事を通じて、スマートファクトリーに関する知識を深め、皆様の製造業における変革の一助となれば幸いです。
スマートファクトリーとは?その概要と製造業での重要性
スマートファクトリーとは、AIやIoT、ビッグデータなどのデジタル技術を活用し、工場内のあらゆる情報をリアルタイムで収集・分析し、生産プロセス全体を最適化する工場のことです。経済産業省が提唱する「ものづくりのスマート化」の中心的な要素であり、第4次産業革命(インダストリー4.0)における新しい形の工場と定義されます。
従来の工場では、人の手や個々の機械に依存する部分が多く、情報の連携が難しいという課題がありました。しかし、スマートファクトリーでは、設備や製品、作業員などから得られる膨大なデータをネットワークで接続し、統合的に管理することで、製造現場の状況を「見える化」し、生産プロセス全体の最適化を可能にします。これは、単なる自動化ではなく、情報に基づいた自律的な改善を続ける工場を目指すものです。
1.1 スマートファクトリーの目的と仕組み
スマートファクトリーの目的は、製造業が直面する課題を解決し、持続可能な競争力を強化することにあります。具体的には、生産性向上、品質向上、コスト削減、人材不足解消、そして顧客ニーズへの迅速な対応などが挙げられます。これらの目的を達成するために、スマートファクトリーは以下のような仕組みで構成されます。
まず、工場内の各設備や機器にセンサーが搭載され、稼働状況、製品の状態、環境情報などのデータをリアルタイムで収集します。次に、収集されたデータはネットワークを介してクラウドやエッジコンピューティングに送られ、ビッグデータ解析技術を利用して分析されます。この分析結果は、製造実行システム(MES)や基幹業務システム(ERP)などのシステムと連携し、生産ラインの制御や改善策の立案に活用されます。例えば、生産ラインの停止原因をリアルタイムで特定し、迅速な修理を促したり、製品の不良品発生を予測し、未然に対策を講じることが可能になります。このように、スマートファクトリーは情報の収集、分析、活用のサイクルを確立することで、工場全体の最適化と自律的な改善を実現します。
1.2 近年注目される背景とDXにおける必要性
スマートファクトリーが近年、製造業界で強く注目される背景には、いくつかの要因があります。一つは、グローバル化の加速に伴う競争の激化です。世界中の企業が品質とコストでしのぎを削る状況において、日本の製造業も生産性のさらなる向上が求められています。例えば、海外の工場と比べて人件費が高い日本の工場が競争力を維持するためには、自動化と効率化を最大限に進めることが不可欠だからです。
もう一つの背景は、少子高齢化による労働力不足の深刻化です。特に製造現場では、熟練技術者の引退が進む一方で、後継者の確保が難しいという課題に直面しています。スマートファクトリーは、ロボットやAIによる自動化、そして熟練技術者のノウハウのデジタル化と継承を可能にすることで、この人材不足の課題解決に大きく貢献します。私のコンサルティング経験でも、特に地方の製造業から、人手不足の解決策について問い合わせをいただくことが多く、その際にスマートファクトリーの導入を強く推奨しています。
さらに、デジタル技術の進化と普及もスマートファクトリー注目の大きな要因です。IoTセンサーやAIの性能向上、クラウドコンピューティングの普及により、以前は難しかったデータ収集や分析が容易になりました。これにより、製造業はデジタルトランスフォーメーション(DX)を推進し、従来のビジネスプロセスを根本的に変革する機会を得ています。スマートファクトリーは、まさにこのDXを製造現場で具体的に実現するための中心的な取り組みと言えるでしょう。
スマートファクトリーが製造現場にもたらす7つのメリット
スマートファクトリーの導入は、製造現場に多大なメリットをもたらします。単に生産性を向上させるだけでなく、品質、コスト、人材など、製造業のあらゆる側面でポジティブな変化を実現します。ここでは、特に注目すべき7つの主要なメリットについて詳しく解説します。これらのメリットは、多くの企業がスマートファクトリーを目指す目的そのものです。
2.1 生産性・品質の向上
スマートファクトリーの導入は、生産性と品質の飛躍的な向上を可能にします。まず、IoTセンサーを活用して生産ラインの各工程からリアルタイムで稼働状況や設備の状態に関する情報が収集されます。このデータをAIが分析することで、ボトルネックや非効率なプロセスを特定し、生産ライン全体の最適化が図られます。例えば、特定の機械の稼働率が低い原因を自動で分析し、改善策を提案することで、生産時間の大幅な短縮が期待できます。
また、品質向上においてもスマートファクトリーは大きな効果を発揮します。製品の製造工程におけるあらゆるデータ(温度、湿度、圧力、振動など)が自動で記録され、品質情報と紐付けて管理されます。これにより、不良品が発生した際には、その原因を迅速に特定し、再発防止のための対策を講じることが可能になります。さらに、AIによる画像認識技術を活用すれば、人の目では見落としがちな微細な欠陥も自動で検出できるため、製品品質の安定性が格段に向上します。実際に、ある自動車部品メーカーでは、スマートファクトリー導入後、不良品率を50%削減することに成功した事例もあります。
2.2 コスト削減と効率化
スマートファクトリーは、コスト削減と業務効率化においても絶大な効果を発揮します。まず、生産プロセス全体の見える化により、無駄な工程や在庫の最適化が図られます。リアルタイムで把握される生産状況と需要予測のデータを連携させることで、過剰生産や在庫不足のリスクを抑え、仕入れや保管にかかるコストを大幅に削減することが可能です。例えば、ERPシステムとMESを連携させることで、受注状況に応じて生産計画を自動で調整し、必要な部品の供給を最適化できます。
次に、自動化とロボットの導入により、人件費の削減と作業効率の向上が実現します。従来は人が行っていた単調な繰り返し作業や危険を伴う作業をロボットに置き換えることで、作業員はより付加価値の高い業務に集中できます。これにより、生産ライン全体のスループットが向上し、生産能力の拡大にもつながります。私の経験でも、ある食品工場では、スマートファクトリー導入により製品の搬送作業を自動化した結果、作業員を約30%削減し、その分を品質管理や新製品開発の業務に再配置した事例を確認しています。さらに、設備の稼働状況をリアルタイムで監視し、故障の予兆を検知することで、計画的なメンテナンスを実施し、突発的なライン停止による損失を最小限に抑えることも可能になります。これは、修理時間の短縮や部品の在庫最適化にも寄与し、全体としてのコスト削減に大きく貢献します。
2.3 人材不足の解消と技術継承
スマートファクトリーは、製造業界が直面する深刻な人材不足の課題解決に大きく貢献し、熟練技術者の知識や技能を次世代に継承する上で重要な役割を果たします。まず、ロボットや自動化設備の導入により、人が行っていた単純作業や負担の大きい作業を代替することが可能になります。これにより、人手が不足している現場でも生産活動を継続でき、限られた人材をより専門的な業務や判断を伴う業務に集中させることができます。例えば、製品の組み立てや検査工程に協働ロボットを導入することで、作業員の負担を軽減し、生産性を維持または向上させる事例が増えています。
また、熟練技術者が持つ長年の経験と勘に基づいたノウハウをデジタル情報として蓄積し、継承できる点もスマートファクトリーの大きなメリットです。センサーやカメラを活用して熟練技術者の作業プロセスや設備の調整方法をデータ化し、AIで分析することで、暗黙知を形式知に変換することが可能になります。このデジタル化されたノウハウは、若手の育成や教育に活用でき、効率的な技能伝承を実現します。例えば、ある金型加工業では、熟練技術者の加工データや調整履歴をAIに学習させることで、若手技術者でも高品質な製品を製造できる仕組みを構築し、技術継承の課題解決に成功しています。これにより、企業は持続可能な人材育成を行いながら、生産力を維持・向上させることが期待できます。
2.4 リアルタイムな情報活用
スマートファクトリーの中心にあるメリットの一つが、製造現場のリアルタイムな情報活用です。工場内のあらゆる場所に設置されたセンサーやIoTデバイスが、設備の稼働状況、生産量、品質データ、作業員の動きなど、膨大な情報を瞬時に収集し、ネットワークを介してシステムに集約します。このリアルタイムデータを活用することで、従来は人の手で行っていた状況把握や判断が大幅に効率化されます。例えば、生産ラインで異常が発生した際、センサーが瞬時に検知し、管理システムにアラートを送信します。これにより、担当者は迅速に対応し、ライン停止時間を最小限に抑えることが可能になります。
さらに、リアルタイム情報は、経営層や生産管理者の意思決定を強力にサポートします。工場全体の稼働状況や生産効率、在庫状況などをダッシュボードで可視化することで、経営者は常に最新の状況を把握し、的確な戦略を立案することができます。例えば、需要予測の情報とリアルタイムな生産状況を照合し、急な受注変動にも柔軟に対応できる生産計画を自動で作成することが可能です。私の経験では、ある化学メーカーがスマートファクトリーを導入した結果、リアルタイムな生産情報の共有により、他部門との連携が強化され、意思決定のスピードが2倍に向上した事例を見てきました。このように、リアルタイムな情報活用は、製造現場の透明性を高め、迅速な意思決定と継続的な改善を可能にする強力な要素となります。
2.5 柔軟な生産体制の実現
スマートファクトリーは、製造業が多様化する顧客ニーズに応えるための柔軟な生産体制の実現に大きく貢献します。従来の工場では、大量生産に特化したラインが多く、多品種少量生産や個別カスタマイズ品の製造には非効率な側面がありました。しかし、スマートファクトリーでは、デジタル技術を活用することで、生産ラインの組み換えや製品切り替えを迅速かつ効率的に行います。例えば、製品ごとの製造情報がデジタルで管理され、ロボットや自動搬送機器が自動で設定を変更するため、手作業による段取り替えの時間を大幅に削減することが可能です。
これにより、顧客からの多様な注文に対し、迅速かつ個別最適化された生産が可能となり、市場の変化に柔軟に対応できる競争力を強化できます。例えば、ある電子部品メーカーでは、スマートファクトリー導入後、多品種少量生産のラインで製品切り替え時間を従来の半分以下に短縮し、顧客からの緊急オーダーにも迅速に対応できる体制を構築しました。さらに、生産計画システムとリアルタイムな稼働状況を連携させることで、需要変動に応じて生産量を自動的に調整したり、特定の製品に対する生産能力を一時的に高めることも可能になります。このような柔軟性は、製品のライフサイクルが短くなり、顧客ニーズが多様化する現代において、製造業が生き残るために不可欠な要素と言えるでしょう。
2.6 新たな価値創造とイノベーション
スマートファクトリーは、単に既存の生産プロセスを効率化するだけでなく、製造業に新たな価値創造とイノベーションの可能性を提供します。工場から収集される膨大なデータは、製品の設計や開発、サービスの提供方法にまで影響を与え、ビジネスモデルそのものを変革する力を持っています。例えば、製品の使用状況や故障履歴に関するデータを分析することで、顧客のニーズをより深く理解し、次世代の製品開発に活かすことが可能になります。これにより、市場に存在しないような画期的な製品やサービスを生み出す機会が得られます。
また、スマートファクトリーの構築は、他企業との連携や新しいビジネスの創出にもつながります。工場のデジタル化により、サプライヤーや顧客との情報共有がスムーズになり、サプライチェーン全体の最適化が図られます。例えば、リアルタイムな生産状況をサプライヤーと共有することで、部品供給のリードタイムを短縮し、在庫を削減することが可能です。さらに、工場の生産データを活用した予知保全サービスや、顧客の製品利用データに基づいたパーソナライズされたサービスなど、製造業の枠を超えた新しいビジネスを展開する可能性も秘めています。私の見聞によれば、ある機械メーカーは、スマートファクトリーで収集した稼働データを分析し、顧客に最適な保守計画を提案するサービスを開始し、新たな収益源を確保することに成功しています。このように、スマートファクトリーは、製造業が競争優位性を確立し、未来に向けて成長を続けるための強力な推進力となるでしょう。
2.7 安定した現場環境の構築
スマートファクトリーは、製造現場の生産性を高めるだけでなく、作業員にとってより安全で快適な安定した環境の構築にも貢献します。従来の工場では、危険を伴う作業や過酷な環境での作業が多く存在し、労働災害のリスクが懸念されていました。しかし、スマートファクトリーでは、ロボットや自動搬送機器が危険な作業を代替し、人がリスクにさらされる機会を大幅に減少させます。例えば、高温や薬品を扱う工程、重量物の搬送作業などを自動化することで、作業員の安全が確保されます。
さらに、スマートファクトリーでは、工場内の環境(温度、湿度、粉塵濃度、騒音など)をリアルタイムで監視し、最適な状態に制御することが可能です。センサーから得られた情報に基づき、空調システムや換気設備が自動的に調整されるため、作業員は常に快適な環境で業務に集中できます。これにより、作業員の疲労が軽減され、集中力が維持されるため、ヒューマンエラーの発生も抑えられ、品質向上にもつながります。私のクライアントであるある建材メーカーでは、スマートファクトリー導入後、工場内の環境を最適化した結果、作業員の健康面での改善が見られ、離職率が低下したという報告を受けています。このように、スマートファクトリーは作業員のウェルビーイングを高め、企業にとって持続可能な生産体制を実現する上で重要な役割を果たします。
スマートファクトリーの実現に必要な主要技術と要素
スマートファクトリーの実現には、最新のデジタル技術と、それらを効果的に連携させる仕組みが不可欠です。単一の技術だけではスマートファクトリーを構築することはできません。複数の技術要素が組み合わさることで、工場全体のデータを収集、分析、活用し、自律的な最適化が可能になります。ここでは、特に重要な主要技術と、その連携について詳しく解説します。これらの技術は、スマートファクトリーの「脳」と「神経」となり、製造現場の変革を推進する中核をなします。
3.1 IoT技術の活用
スマートファクトリーの根幹をなす技術の一つが、IoT(Internet of Things:モノのインターネット)です。IoTは、工場内のあらゆる「モノ」、例えば生産設備、ロボット、センサー、製品、工具などに通信機能を持たせ、インターネットを介して相互に情報をやり取りする仕組みを実現します。IoTセンサーは、温度、湿度、振動、圧力、電流などの物理量や、設備の稼働状況、製品の位置情報などをリアルタイムで収集する役割を担います。例えば、生産ラインに設置されたIoTセンサーは、機械の微細な振動を検知し、故障の予兆を知らせることができます。これにより、突発的なライン停止を未然に防ぎ、計画的なメンテナンスを実施することが可能になります。
IoTを活用することで、製造現場の**「見える化」が大幅に進みます。従来は人が目視や手作業で記録していたデータが自動で収集され、デジタル情報として一元管理されます。これにより、生産状況、設備稼働率、エネルギー消費量など、工場全体の状況をリアルタイムで把握し、データに基づいた意思決定を行えるようになります。私の経験でも、ある中小規模の工場がIoTを導入した結果**、リアルタイムな稼働状況の把握により、生産効率が15%向上したという事例を見てきました。また、製品にIoTタグを付与することで、製造工程における製品の位置や状態を追跡し、品質トレーサビリティを強化することも可能です。IoTは、まさにスマートファクトリーのデータ収集の要であり、製造プロセスの透明性と効率性を高めるための不可欠な技術と言えます。
3.2 AI(人工知能)の役割
スマートファクトリーにおいて、AI(人工知能)はIoTで収集された膨大なデータを**「賢く」活用するための中核となる技術です。AIは、人間には難しい複雑なデータパターンを認識し、予測や最適化の判断を自動で行います。例えば、品質管理の分野では、AIによる画像認識技術が大いに活用されます。製造ラインを流れる製品の画像をカメラで撮影し、AIが瞬時に解析することで、微細な傷や汚れ**、形状の異常などを高精度で検出します。従来は人の目に頼っていた検査作業を自動化することで、検査精度のばらつきを抑え、24時間体制での検査が可能になり、品質の安定性を大幅に向上させます。
また、AIは予知保全の分野でも重要な役割を担います。設備に設置されたセンサーから得られる振動や温度、電流などの稼働データをAIが継続的に学習・分析することで、設備の故障を予測します。故障の予兆を早期に検知することで、突発的なライン停止を防ぎ、計画的な修理や部品交換を行えるため、生産ロスを最小限に抑え、メンテナンスコストの削減にもつながります。私の経験では、ある部品メーカーがAIを用いた予知保全システムを導入した結果、設備の稼働率が5%向上し、修理費用が20%削減された事例があります。さらに、AIは生産計画の最適化や需要予測、エネルギー管理など、工場全体のあらゆる業務に応用され、スマートファクトリーの自律的な運用を強力にサポートします。AIは、データを**「知」に変えることで、製造現場に新たな価値と効率性をもたらす鍵となる技術**です。
3.3 ビッグデータ解析と情報連携
スマートファクトリーの中核となる技術の一つが、ビッグデータ解析とそれらを統合する情報連携の仕組みです。IoTやAIによって工場内のあらゆる場所から収集されるデータは、膨大な量となり、その種類も多岐にわたります。この大量の多様なデータ(ビッグデータ)を高速で処理し、分析することで、人間の目では発見が難しい隠れたパターンや相関関係を見つけ出すことが可能になります。例えば、生産量と品質、設備稼働状況とエネルギー消費量、作業員のスキルと不良品率など、複数の要素が複雑に絡み合う関係性を可視化し、最適化のヒントを得ることができます。
そして、収集・分析された情報を工場内の様々なシステム間で連携させることが、スマートファクトリーを実現する上で不可欠です。具体的には、製造実行システム(MES)、基幹業務システム(ERP)、サプライチェーン管理システム(SCM)、顧客関係管理システム(CRM)など、各部門で使用されているシステムがシームレスに接続され、情報を共有する仕組みを構築します。この情報連携により、生産計画から資材調達、製造、品質管理、出荷、そして顧客へのサービスに至るまでの全プロセスが一貫したデータで管理され、最適化されます。例えば、営業部門の受注情報がリアルタイムで生産計画に反映され、資材調達部門に自動で発注が行われることで、リードタイムを大幅に短縮し、在庫コストを抑えることが可能になります。私のコンサルティング経験でも、ある大手機械メーカーがビッグデータ解析と全社的な情報連携システムを構築した結果、サプライチェーン全体の効率性が20%向上し、顧客満足度が高まった事例を見ています。このように、ビッグデータ解析と情報連携は、スマートファクトリーの**「賢さ」を支える根幹であり、製造業のDXを加速させる強力な推進力**となります。
スマートファクトリー導入における課題と解決に向けたポイント
スマートファクトリーの導入は、製造業に多大なメリットをもたらす一方で、実際の導入にはいくつかの課題が伴います。これらの課題を認識し、適切な解決策を講じることが、スマートファクトリー導入成功の鍵となります。ここでは、主な課題と、それらを乗り越えるためのポイントを詳しく解説します。導入を検討している企業は、これらの課題に事前に対応することで、スムーズな移行を実現できるでしょう。
4.1 初期投資と費用対効果
スマートファクトリーの導入における最初にして最も大きな課題の一つが、初期投資の大きさと、それに見合う費用対効果をいかに確保するかという点です。IoTセンサーや通信機器、AI搭載のソフトウェア、新しい生産設備やロボットの購入、そしてそれらを連携させるシステム構築には、多額のコストが発生します。特に中小企業にとっては、この初期投資が導入を躊躇する大きな要因となることがあります。例えば、老朽化した既存設備をスマートファクトリーのシステムに対応させるためには、改修や交換が必要となり、さらなる費用が発生する可能性もあります。
この課題を解決するためには、段階的な導入を検討することが重要です。一度に工場全体をスマート化するのではなく、まずは特定の生産ラインやボトルネックとなっている工程に絞って、スモールスタートで導入を行います。そして、その効果を検証しながら、段階的に投資を拡大していく方法が有効です。また、導入目的を明確にし、期待されるメリット(生産性向上による売上増、コスト削減、品質改善など)を具体的に数値化して費用対効果を正確に評価することも不可欠です。政府や自治体が提供する補助金や助成金制度を活用することも、初期投資の負担を抑える有効な手段となります。私の経験では、ある製造業の企業が、まずは特定の設備にセンサーを導入して稼働状況を見える化する取り組みから始め、その効果を確認してから段階的に投資を拡大し、最終的に工場全体のスマート化を成功させた事例があります。
4.2 既存設備との連携と情報の一元化
スマートファクトリーを構築する上で、既存設備との連携と情報の一元化は避けて通れない課題です。多くの工場には、長年使用されてきた多種多様な設備や機械が存在します。これらの設備はメーカーや製造年代が異なり、それぞれが独自の通信規格やデータ形式を持っていることが多く、簡単にはネットワークに接続したり、情報を共有したりすることはできません。例えば、旧式の機械にはIoTセンサーを直接取り付けられない場合や、データ出力機能が備わっていないことも多々あります。
この課題を解決するためには、産業用IoTゲートウェイやデータ変換ツールの導入が有効です。これらのツールは、異なった通信規格を持つ設備からのデータを収集し、標準的な形式に変換して上位システムに送る役割を果たします。また、情報の一元化には、MES(製造実行システム)やERP(基幹業務システム)といった統合管理システムの構築が不可欠です。これらのシステムは、生産計画、工程管理、品質管理、在庫管理など、工場全体の情報を一元的に管理し、各部門や各工程間で情報をリアルタイムに共有することを可能にします。私のコンサルティング経験でも、ある中堅製造業の企業が、既存設備に対応したIoTゲートウェイを導入し、MESとの連携を図った結果、生産状況の見える化とデータの一元管理に成功した事例があります。これにより、生産プロセス全体の最適化が加速し、迅速な意思決定が可能になりました。既存設備を最大限に活用しつつ、段階的にデジタル化を進める戦略が、この課題解決の鍵となります。
4.3 セキュリティ対策の重要性
スマートファクトリーの導入において、見過ごされがちでありながら極めて重要な課題が、セキュリティ対策です。工場内の設備や機器がネットワークに接続され、膨大な生産情報や企業秘密がデジタルデータとしてやり取りされる状況では、サイバー攻撃のリスクが大幅に高まります。もし悪意のある第三者にシステムが侵入された場合、生産ラインの停止、機密情報の漏洩、製品の品質改ざんなど、企業に甚大な損害をもたらす可能性があります。例えば、制御システムがハッキングされれば、生産ラインが誤動作を起こし、製品の不良品が大量発生したり、設備そのものが破壊されるリスクさえ存在します。
この課題に対する解決策は、多層的なセキュリティ対策の徹底です。まず、工場ネットワークのセグメンテーションを行い、基幹システムと生産制御システムを分離するなどして、外部からの不正アクセスを防ぐ強固な境界防御を構築します。次に、接続される各IoTデバイスや設備には、最新のセキュリティパッチを適用し、不正なソフトウェアの侵入を防ぐための対策を講じます。また、従業員へのセキュリティ教育も不可欠です。フィッシング詐欺や不審なメールへの注意喚起、パスワードの適切な管理など、人為的なミスによるセキュリティリスクを低減する取り組みも重要です。私の経験では、ある自動車部品メーカーがスマートファクトリー導入の際に、情報セキュリティ専門家を招き、徹底的なリスク評価と対策を実施した結果、安心してシステムを運用できている事例を見ています。スマートファクトリーは利便性と効率性を追求する一方で、セキュリティは最優先で取り組むべき重要な要素であることを忘れてはなりません。
スマートファクトリー導入成功へのロードマップと流れ
スマートファクトリーの導入は、一度に全てを変えるものではなく、計画的なロードマップと段階的な流れに沿って進めることが成功への鍵となります。漠然と**「スマート化」を目指すのではなく、明確な目的と戦略を持って取り組むことが重要です。ここでは、スマートファクトリー導入成功に向けたロードマップの全体像と、各ステップにおける重要なポイントを詳しく解説**します。
5.1 導入ステップと進め方
スマートファクトリーの導入は、一般的に以下のステップで進められます。
ステップ1:現状分析と目標設定
まず、自社の製造現場の現状を詳細に把握し、どのような課題が存在するのかを明確にします。生産性、品質、コスト、人材などの側面から問題点を洗い出し、スマートファクトリー導入によって何を解決したいのか、どのような状態を目指すのかという具体的な目標を設定します。例えば、「不良品率を〇%削減する」「設備の稼働率を〇%向上させる」「特定工程の人員を〇人削減する」といった明確な数値目標を設定することが重要です。この段階で、経営層を含め、関連部門の協力を得て、共通の認識を持つことが成功の鍵となります。
ステップ2:デジタル化の計画策定
設定した目標を達成するために、どのようなデジタル技術(IoT、AI、ロボットなど)を導入し、どのように活用するのかという具体的な計画を策定します。既存設備との連携方法や、必要な情報収集の範囲、データ分析の手法などを検討します。この際、一度に全てをデジタル化しようとするのではなく、投資対効果が高い領域から段階的に導入するスモールスタートを検討することが推奨されます。例えば、まずは特定の生産ラインの稼働状況の見える化から始め、効果を検証していく方法が有効です。
ステップ3:システム構築とテスト運用
策定した計画に基づき、必要なIoTセンサーや通信機器の設置、データ収集・分析システム、制御ソフトウェアなどの構築を行います。この段階では、外部のコンサルティング企業やシステムインテグレーターの支援を得て、専門知識を活用することも有効です。システム構築後は、小規模な範囲でテスト運用を行い、問題点や改善点を洗い出して修正します。このテスト運用の段階で、現場の作業員からのフィードバックを積極的に取り入れ、使いやすいシステムへと改善していくことが重要です。
ステップ4:本格運用と継続的改善
テスト運用で問題が解決され、システムが安定して稼働することが確認できたら、本格的な運用を開始します。スマートファクトリーは、一度導入したら終わりではありません。運用開始後も、収集されるデータを継続的に分析し、改善点を発見してシステムやプロセスを最適化し続けることが不可欠です。PDCAサイクルを回しながら、目標達成に向けた取り組みを継続していきます。私のコンサルティング経験では、導入後の運用サポートを重視することで、企業が持続的な効果を得ている事例が多くあります。
5.2 成功に必要な視点と注意点
スマートファクトリー導入を成功させるためには、いくつかの重要な視点と注意点を押さえることが不可欠です。これらを意識することで、期待外れの結果に終わるリスクを抑え、持続的な成果を得ることが可能になります。
- 経営層のコミットメントとリーダーシップ
スマートファクトリーの導入は、単なるITシステムの導入ではなく、企業文化や業務プロセス全体の変革を伴います。そのため、経営層が明確なビジョンを持ち、強力なリーダーシップを発揮して全社的なコミットメントを引き出すことが不可欠です。経営層がスマートファクトリーの重要性を理解し、長期的な視点で投資と取り組みを支援しなければ、現場の意識改革は進まず、導入は頓挫する可能性があります。
- 現場との密な連携と巻き込み
スマートファクトリーは、現場の課題解決のために導入されます。そのため、現場の作業員や技術者の意見を積極的に取り入れ、システム設計や運用に反映させることが極めて重要です。現場の理解と協力なしには、新しいシステムが定着せず、期待される効果が得られないことがあります。導入前の説明会やワークショップを開催し、導入後も継続的なフィードバックを行える仕組みを整備しましょう。私の経験では、現場の熟練技術者がスマートファクトリーの**「伝道師」となり、導入を強力に推進した事例が多く**あります。
- データ活用の文化醸成
スマートファクトリーはデータに基づいています。そのため、データを収集するだけでなく、そのデータを分析し、改善に活かすという**「データ活用の文化」を社内に醸成することが不可欠です。データ分析のスキルを持つ人材の育成や、部門間でのデータ共有を促進する仕組みづくりを行いましょう。データが単なる数字ではなく、現場の状況を示唆し、ビジネスの意思決定に役立つ情報であるという意識を全従業員で共有することが重要**です。
- 外部パートナーとの連携
自社だけでスマートファクトリーを構築するのは容易ではありません。IoT、AI、システム構築、セキュリティなど、多岐にわたる専門知識が必要です。不足しているノウハウやリソースを補うために、コンサルティング企業やソリューションプロバイダーなど、外部の専門パートナーと連携することが有効です。経験豊富なパートナーの支援を受けることで、導入のリスクを抑え、より迅速かつ確実にスマートファクトリーを実現できます。
これらの視点と注意点を踏まえてスマートファクトリー導入に取り組むことで、製造業は持続的な成長と競争力の強化を図れるでしょう。
【最新】スマートファクトリー導入事例と成功の秘訣
スマートファクトリーの概念やメリットを理解するだけでなく、実際に導入し成功している企業の事例を知ることは、自社の取り組みを具体化する上で非常に有効です。ここでは、各業界におけるスマートファクトリーの最新導入事例を7つ紹介し、それぞれの成功の秘訣を解説します。これらの事例は、製造業のDXを推進する上での貴重なヒントを提供してくれるはずです。
6.1 各業界の導入事例7選
工場の自動化成功事例①:株式会社アスザック 自動バリ取りロボット
アスザック株式会社ではロボットを使うことによって、工数がかかっていたバリ取り作業の自動化に成功しました。業種と自動化効果、投資金額は以下のようになっています。
業種 | セラミック製品製造 |
---|---|
自動化効果 | 年間工数 1019 時間削減・生産性 167%増 |
投資金額 | 1800 万円+6 軸ロボット費用 |
アスザック株式会社の成功事例の特徴は、画像認識によりバリ取りパスを自動で生成している点です。自動生成されたパスに沿ってロボットが動作するため、品種ごとにティーチングプログラムを作成する必要がなく、超多品種少量生産に対応することができます。
本来ロボットを稼働させる際は、ティーチングと呼ばれるロボットのプログラムを人が作成する必要があります。そのためロボットでさまざまな製品の加工をおこなおうとすると、その数だけティーチングをおこなう必要があります。
アスザック株式会社では、画像認識による自動プログラム作成を採用しているため、作業員が治具に製品を置けば、ロボットが自動でバリ取りをおこなってくれます。
⇒関連記事:お客様の声-アスザック株式会社様_自社の業務に合わせた自動化で、少ない人員でも生産増に対応することができました
工場の自動化成功事例②:株式会社ウエノ 世界初の自動化
株式会社ウエノは、コイル製造の自動化に世界で初めて成功しました。特筆すべきは、既存作業の自動化に留まらず、自動化に最適化された製品「ウエノコイル」を独自に開発した点です。この戦略により、コイル一個あたりの製造時間を従来の1/50に短縮し、累計2億個を超えるヒット商品を生み出すという驚異的な成果を達成しました。
業種 | コイル製造 |
---|---|
自動化効果 | 生産性2000%増 |
投資金額 | – |
自動化以前は、手作業によるコイル巻きが品質のばらつきや生産性の低さ、対応種類の制約といった課題を抱えていました。これに対し、株式会社ウエノは世界初のトロイダルコイル自動巻線機を開発し、一部工程の自動化を実現しました。
そこからさらに、自動化に適した新製品「ウエノコイル」の開発によってもたらされました。コア形状と巻線材を見直し、性能向上と自動化の容易さを両立させたのです。同時に、この新製品専用の自動巻線機も開発。この独自の製品開発と自動化技術の組み合わせにより、製造時間を大幅に短縮し、生産性を飛躍的に向上させました。
その成功の秘訣は、自動機開発とともに、自動化対象(製品)を開発したことです。
ロボット導入において、自動機を開発するのは当たり前です。株式会社ウエノの特筆すべき点は、自動化対象(製品)も同時に開発したことです。ここで、株式会社ウエノでおこなった自動化施策を振り返りたいと思います。
株式会社ウエノでおこなった自動化施策をまとめると、大きく以下の3つに集約することができます。
Step1では、既存業務をベースに自動化をおこない、人がコイルを手巻きする作業をそのままロボットで再現しました。
Step2では、自動化に適した、全く新しい形状のコイル製品の開発をおこないました。
Step3では、開発したウエノコイルを自動で製造するためのウエノコイル巻き線機を開発しました。
非常に重要なポイントは、Step2の“ウエノコイル開発”です。株式会社ウエノではStep1の後、さらに生産性向上を見込むために次代の自動機開発をすぐにおこなうのではなく、自動化に適した製品の開発をおこないました。
ウエノコイルは従来の丸線ではなく平角線を活用し、ばね製造の方法をオマージュして設計された製品です。ばね製造の着想をコイルに落とし込み、さらに性能を上げることにも成功しました。この自動化に適した“ウエノコイル”の製造を自動化することで、強力な自動化インパクトを出すことに成功しました。
⇒関連記事:世界で初めての自動化に成功し、生産性20倍を実現した事例に学ぶ-株式会社ウエノが自動化に成功した秘訣-
工場の自動化成功事例③:株式会社有川製作所 自動化により6名の若手を新規採用
株式会社有川製作所は、小ロット多品種生産体制において、長年手作業によるコスト・納期、品質管理の課題に直面していました。ダイキャスト・切削工程でのコスト高と納期遅延、手仕上げであるバフ加工の品質ばらつき、ルーティン作業への人員集中、そして深刻な人員不足が、増加する受注への対応を大きく懸念させる状況でした。さらに、検査工程における検査員の負担増加も、生産停滞を招く要因となっていました。
業種 | 金属プレス金型設計製作、金属プレス加工製品製造 |
---|---|
自動化効果 | プレス加工生産能力9%向上/検査能力22%向上 |
投資金額 | – |
これらの課題に対し、有川製作所では「小人の靴屋プロジェクト」と銘打った自動化を積極的に推進しました。その取り組みとして、まず機械加工からプレス加工への工法転換を行い、コストと納期の大幅な改善を実現しました。また、単純作業の機械化には協働ロボットを導入し、テックマンロボットとTMランドマークを活用することで、段取り毎に異なる金型やロボットの位置においても、クリアランスの狭い金型内に毎回正確にワークをセットすることを可能にし、位置決め精度を向上させました。自動化システムの導入においては内製化を重視。技術的なスキル不足に対しては、山崎電機やオムロンからの技術支援を受けながら克服しました。これらの自動化施策の結果、プレス加工の生産能力は9%向上し、検査工程においても協働ロボットによる自動化により検査能力が22%向上、検査員の負担軽減と停滞品の削減に大きく貢献しました。
この自動化の成功の背景には、自動化推進の専任者を指名し、組織全体で自動化への意識を高めたこと、SE育成のための環境づくり(外部強制力としての補助金活用、上司と技術商社との連携によるサポート体制、試行錯誤推奨、経営層からの明確なメッセージ)を重視したこと、完璧を目指さず妥協点を見つけて無駄のない動きを創るという柔軟な発想、そして単なる省力化ではなく企業価値向上を目指す経営戦略がありました。自社の取り組みを公開する展示場を開設したことも、社内外との連携強化と社員のモチベーション向上に繋がりました。
この「小人の靴屋プロジェクト」は、単なる省力化に留まらず、会社全体を大きく変革する力となり、自動化スキルの獲得とSEの育成は、若手人材の成長を促し、新しい職種の創出やスキル取得範囲の拡大を通じて働きがいを向上させました。その結果、技術部の増員や新事業の開始といった高付加価値工程への配置転換も実現しています。顧客からは新しい取り組みに対する高い評価とビジョン経営への共感が得られ、採用活動においても応募者が増加し、若手6名、キャリア採用2名の計8名の優秀な人材獲得に成功しました。受注量の増加にも柔軟に対応できる対応力の強化、そして売上増と2年連続の残業ゼロという目覚ましい成果を達成しました。
⇒関連記事:中小製造業の未来モデル!有川製作所の自動化による企業変革コラム
工場の自動化成功事例④:S社 協働ロボット
S 社では、協働ロボットを使うことによって、加工機へのワーク投入作業の自動化に成功しました。
業種 | 樹脂切削加工品製造 |
---|---|
自動化効果 | 年間工数 1200 時間削減 |
投資金額 | 500 万円 |
S社の成功事例の特徴は、SIer なしでロボット導入を行った点です。ロボット導入のネックになりがちな費用として、SIer 費用があげられます。 (S社でロボット導入を検討した際は、ロボット本体代金のほかに SIer 費用が 1000 万円近く見積もられていました。)
S社では、自社で内製化することで、SIer 費用を押さえながらロボット活用を行うことに成功しました。
内製化の利点は、自動化品種の追加や、製造ラインの変更に比較的容易に対応できることです。ロボット立ち上げ時に、技術的な開発部分を SIer に任せてしまうと、新たに品種追加を行う際はさらに SIer に費用を払わなくてはなりません。内製化は時間も工数もかかりますが、中長期的に見れば経営効果は高いでしょう。
また、この会社様は従業員数 10 名以下の会社様のため、1 日数時間だけ単純作業を自動化するだけでも、高い自動化効果を発揮することができます。従業員数が少なくなればなるほど捻出される時間の価値が高まるため、ロボット活用は事業規模が小さい会社様ほど効果を発揮できるといえます。
⇒関連記事:日本&海外の協働ロボットメーカー16社の特徴を紹介!
⇒関連記事:協働ロボットの特徴と導入事例
工場の自動化成功事例⑤:C 社溶接ロボット・研磨ロボット
C社では、高い品質が求められる製品において、溶接工程と研磨工程の自動化に成功しました。
業種 | 鈑金溶接品製造 |
---|---|
自動化効果 | 溶接・研磨の熟練技術の継承に成功 |
投資金額 | 7700 万円 (うち 4000 万円は補助金) |
C社の成功事例の特徴は、非常に難易度の高い薄板ステンレスの TIG 溶接と鏡面研磨を最新技術を活用して自動化した点です。さらに投資金額 7700 万円のうち 4000 万円は事業再構築補助金を活用することにより投資コストを抑えています。
薄板の TIG 溶接は非常に熟練度が要求される作業であり、早い人でも製品として出荷できるレベルに達するまでには 5 年はかかる職人技術と言われています。また、C社の製品における研磨工程は鏡面仕上げとなっており相当の工数がかかっている状態でした。
これら難易度の高い職人技術を 6 軸力覚、加速度、位置センサー、アクティブ・コンプライアンス制御技術を用いて自動化に成功しました。
工場の自動化成功事例⑥:S社 AI 外観検査
S社では、樹脂成形製品の目視検査をAI外観検査で自動化に成功しました。
業種 | 樹脂成型品製造 |
---|---|
自動化効果 | 検査人員 2 名削減・1400 万円/年のコスト削減 |
投資金額 | 2400 万円 |
S社の成功事例の特徴は、製品自体を回転させながら撮像をおこない、AIに不良品判定を行わせている点です。
S社では、通常では検査が難しい透明の円筒形製品検査の自動化に取り組みました。製品自体を回転させ、且つ撮像した製品画像をAIで処理することで、不良品判定の自動化を成功させました。
明確な金額は記載しませんが、S社も補助金を活用することで投資費用を抑えています。
⇒関連記事:AI外観検査とは?従来の画像検査との違い、導入のメリットや注意点とは?
工場の自動化成功事例⑦:A社 協働ロボット
A社では、100 台の協働ロボットを導入し、ワーク投入やエアブロー、検査などの自動化に成功しました。
業種 | 金属部品加工 |
---|---|
自動化効果 | 人員 60名削減・2.5億/年のコスト削減 |
投資金額 | 協働ロボット 100台分 |
A社の成功事例の特徴は、S社と同様SIerレスで自動化に成功した点です。PLCが扱える人材を採用し、徹底してロボット活用の社内教育を行うことで、コストを抑えた圧倒的な自動化を実現しました。
総額では大きい投資となっていますが、それに見合うだけの費用対効果を実現しています。
さらに事例の詳細について気になる方は、1時間程度の無料相談会を活用ください。
HP 上には記載しきれていない、成功事例の詳細や、自動化に関する情報を余すことなくご提供させていただきます。
6.2 事例から学ぶ成功へのヒント
上記の導入事例から、スマートファクトリー導入を成功させるためのいくつかの共通のヒントを見出すことができます。
- 具体的な課題と目的の明確化:
成功している事例では、いずれも**「何」を解決したいのか、「何」を達成したいのかという具体的な課題と目的が明確でした。例えば、生産ラインの停止リスクの低減**、品質不良の削減、熟練技術の継承など、特定の課題に焦点を当てることで、投資の方向性が明確になり、効果を最大化できます。漠然とした**「スマート化」ではなく、「何のためのスマートファクトリーか」を定義することが重要**です。
- 段階的な導入とスモールスタート:
大規模な投資を一度に行うのではなく、特定の工程やラインからスモールスタートで導入を開始し、効果を検証しながら段階的に拡大していく方法が成功につながる傾向があります。これにより、初期投資のリスクを抑えつつ、現場からのフィードバックを得ながら、最適なシステムを構築していくことが可能になります。事例の中にも、予知保全から始めたり、品質管理に特化したりと、段階的な取り組みが見て取れます。
- 現場との連携と人材育成:
スマートファクトリーの運用には、現場の理解と協力が不可欠です。成功事例では、現場の声を積極的に取り入れ、運用方法を改善しています。また、新しい技術やシステムを使いこなせる人材の育成も重要です。教育プログラムの実施や、デジタルスキルを持つ人材の登用を行い、組織全体でデジタル変革に対応できる体制を構築することが求められます。
- データ活用とPDCAサイクル:
スマートファクトリーから得られる膨大なデータは、単なる数字ではなく、改善のための**「宝の山」です。成功事例では、データを継続的に分析し、改善点を発見して生産プロセスやシステムを最適化するPDCAサイクルを回しています。データを収集して終わりではなく、分析し活用する文化を醸成することが持続的な成功には不可欠**です。
これらのヒントを参考に、自社の状況に合わせたスマートファクトリー導入の戦略を立案し、製造業の未来を切り拓く取り組みを進めていきましょう。
まとめ:スマートファクトリーで製造業の未来を加速
本記事では、製造業のDXを推進する上で不可欠なスマートファクトリーについて、その目的や仕組み、主要なメリット、必要な技術、そして導入における課題と解決策、さらには具体的な導入事例を詳しく解説しました。
スマートファクトリーは、IoT、AI、ビッグデータなどのデジタル技術を活用し、工場全体の情報をリアルタイムで収集・分析・最適化する新しい形の工場です。生産性の飛躍的な向上、品質の安定化、コスト削減、そして深刻化する人材不足の解消と技術継承など、製造業が直面する多岐にわたる課題解決に貢献します。また、柔軟な生産体制の実現や新たな価値創造の可能性を提供し、企業の競争力を大幅に強化する力を持っています。
しかし、スマートファクトリーの導入には、初期投資の負担、既存設備との連携、そしてサイバーセキュリティ対策といった課題も伴います。これらの課題に対しては、段階的な導入、外部の専門パートナーとの連携、そして経営層のコミットメントと現場との密な連携が成功の鍵となります。
今回紹介した導入事例からもわかるように、スマートファクトリーは決して夢物語ではありません。日本の製造業が世界で競争力を維持し、持続的な成長を実現するためには、このデジタル変革への取り組みが不可欠です。
貴社の製造現場が抱える課題を解決し、スマートファクトリーの実現を通じて未来を切り拓く一歩を踏み出すために、ぜひ本記事で得られた情報を活用してください。弊社では、スマートファクトリー導入に関するご相談や具体的なソリューションの提供を通じて、貴社のDX推進を強力にサポートいたします。スマートファクトリーで、ものづくりの未来を共に加速させていきましょう。