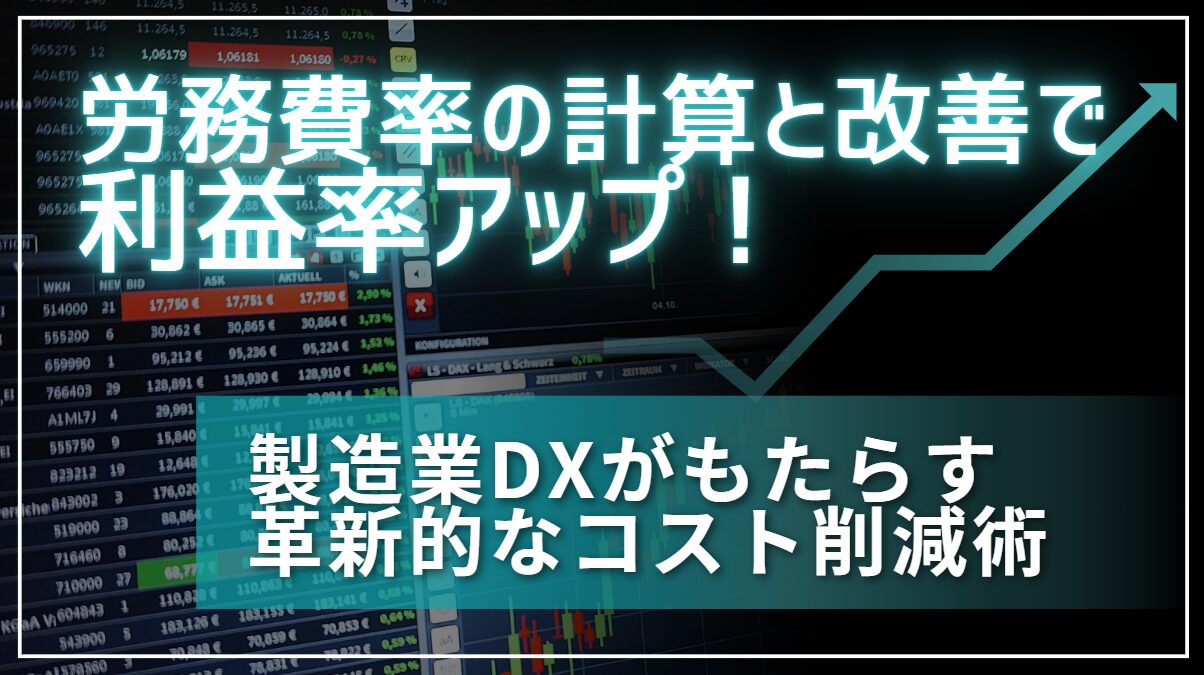
労務費率の計算と改善で利益率アップ!製造業DXがもたらす革新的なコスト削減術
2025.08.21
はじめに
製造業の経営を考える上で、人件費は避けて通れないコストです。しかし、「社員の頑張りをコストと見なすのは忍びない」「人件費を削減すると、社員のモチベーションが下がってしまうのではないか」といった葛藤を抱えている経営者の方も少なくありません。
そこで重要になるのが、「労務費率」という指標です。この指標を正しく理解し、コントロールすることは、単なるコスト削減ではなく、企業の利益率を向上させ、競争力を高めることにつながります。この記事では、労務費率の基礎知識から、多くの企業が直面するデータ取得の課題、そしてそれを解決する「製造業DX」の具体的な手法まで、成功事例を交えて徹底的に解説します。
1. 利益率改善の鍵「労務費率」とは?製造業における重要性を再認識
製造業において、労務費率は経営の健康状態を測るための重要な羅針盤です。まずは、その基本的な定義と、なぜこれほどまでに注目すべき指標なのかを解説します。
1-1. そもそも「労務費」とは?人件費との違いを明確に理解する
労務費と人件費は混同されがちですが、会計上は明確に区別されます。
人件費 企業の従業員全体にかかる費用。給与や賃金、賞与、退職金、法定福利費(社会保険料など)のすべてを含みます。
労務費 人件費のうち、製品の製造に直接的・間接的に関わる人件費のみを指します。
つまり、工場で働く製造スタッフの給与は「労務費」に含まれますが、経理や営業、事務スタッフの給与は「労務費」には含まれず、「販売費及び一般管理費」として計上されます。
以下に、労務費と人件費の関係を図解で示します。
1-2. 製造業における「労務費率」の正しい計算方法
労務費率は、売上高に対する労務費の割合を示す指標です。製品の製造にかかる人件費が、売上に対してどれくらいの割合を占めているかを可視化できます。
労務費率(%) = 労務費 ÷ 売上高 × 100
この計算式を分解すると、労務費は「直接労務費」と「間接労務費」に分けることができます。
直接労務費: 特定の製品の製造に直接かかった賃金。例えば、組み立て作業員や加工技術者の賃金など。
間接労務費: 製造に間接的にかかった賃金。例えば、工場全体の管理者の給与や、特定の製品に関わらない清掃員の賃金など。
自社の労務費を正確に把握するためには、これらの内訳を細かく分類して管理することが不可欠です。
参考レポート:「【製造業 原価管理】時流予測レポート2025 (今後の見通し・業界動向・トレンド)」
https://www.funaisoken.co.jp/dl-contents/jy-cost_S045?media=smart-factory_S045
1-3. 労務費率はなぜ重要?経営者が注目すべき2つの理由
労務費率が経営にとって重要である理由は、主に以下の2つです。
製造原価の大部分を占めるため、コスト管理の要となる
◦製造原価は「材料費」「労務費」「経費」の3つで構成されます。多くの製造業では、この中で労務費が占める割合が非常に高く、労務費をコントロールすることが、製造原価全体の管理に直結します。
生産性の改善度合いを測る重要な指標となる
◦労務費率が高いということは、売上に対して人件費の負担が大きいことを意味します。これは、生産性が低い、つまり「同じ売上を上げるのに、より多くの人手と時間がかかっている」状態を示唆します。労務費率を改善することは、生産性を向上させることと同義です。
2. ほとんどの製造業が抱える課題:労務費のデータ取得が難しい理由
多くの経営者が労務費率の重要性を認識しているにもかかわらず、その改善に踏み切れない大きな壁があります。それは、労務費の元となる「作業実績」データの取得が難しいという現実です。
2-1. 「紙の日報」では正確な作業実績が把握できない現実
製造現場では、いまだに多くの企業が紙の日報に頼って作業実績を記録しています。しかし、このアナログな手法には、以下のような問題が潜んでいます。
手書きによる記録のばらつき:
◦作業者が「大体の時間」で記入するため、実際の作業時間との間に乖離が生じやすいです。
◦「加工」「組み立て」といった大まかなカテゴリでしか記録されず、具体的な作業内容や、何にどれだけの時間がかかったのかが不明瞭になります。
これにより、日報のデータは現場の正確な状況を反映しない「不正確なデータ」となり、その後の経営判断を誤らせる原因となります。
2-2. データが不正確だと「見積もりと実際の利益」が一致しない
不正確な労務費データは、深刻な経営課題を引き起こします。
製品ごとの採算性が不明瞭になる:
◦紙の日報では、製品ごとの正確な作業時間がわからないため、個別の原価を算出することが困難です。結果として、見積もり段階では利益が出るはずだったのに、実際には赤字になっていた、という事態が起こりえます。
「勘と経験」に頼った経営から抜け出せない:
◦正確なデータがないため、「この製品は利益が出ているはず」「この作業はムダが多い」といった感覚的な判断に頼らざるを得ません。これでは、科学的な根拠に基づいた経営改善は不可能です。
3. 労務費率を改善する前に!避けるべき「コスト削減のワナ」
労務費率の改善と聞いて、まず「人件費を減らす」「残業をなくす」といった安易なコストカットを思い浮かべる方もいるかもしれません。しかし、これらはかえって企業に大きなダメージを与える可能性があります。
3-1. 安易な人件費削減は生産性低下を招く
給与の引き下げや人員整理は、一時的な労務費率の改善にはなるかもしれません。しかし、長期的に見れば、社員のモチベーション低下や技術力の流出を招き、結果的に生産性を大きく低下させます。特に熟練技術者の流出は、企業の競争力そのものを失わせる危険性があります。
3-2. 設備投資は「利益率向上」に繋がるか?費用対効果の見極め方
「労務費削減のために最新の機械を導入しよう」と考えることもあるでしょう。しかし、その投資が本当に利益率向上につながるかは慎重な見極めが必要です。多額の設備投資を行ったにもかかわらず、稼働率が上がらず、新たなコスト負担だけが増えてしまう失敗例も少なくありません。重要なのは、投資が「現場のボトルネック解消」や「高付加価値化」にどう貢献するかを明確にすることです。
4. 利益率を最大化する「製造業DX」による労務費率改善の具体策
前述の課題を解決し、労務費率を根本から改善するために最も効果的なのが「製造業DX」です。ここでは、DXがもたらす革新的な改善策を具体的に解説します。
4-1. リアルタイムデータ可視化による正確な工数管理
最も効果的なのは、現場の作業をリアルタイムでデータ化し、正確な工数を把握することです。IoTセンサーやデジタル日報システムを導入することで、以下のことが可能になります。
正確な稼働時間の記録:
◦機械の稼働状況や作業者の動きを自動で記録し、手書き日報で発生する「勘」や「ばらつき」を排除します。
作業内容の見える化:
◦どの製品のどの工程に、どれだけの時間がかかっているかを正確に把握できます。これにより、見積もり段階での工数と実績を比較し、精度の高い原価管理が可能になります。
4-2. データの見える化で「ムダ」を発見し、生産性を向上させる
リアルタイムで収集したデータは、単なる記録ではありません。分析することで、現場に潜む様々な「ムダ」を発見し、生産性向上に直結する知見を得られます。
生産ラインのボトルネック特定:
◦データにより、特定の工程で作業が滞っている「ボトルネック」を可視化できます。
不良率の根本原因分析:
◦いつ、どの工程で、どのような不良が発生しているかをデータで追跡することで、不良の原因を特定し、対策を講じることができます。これにより、手直しや廃棄にかかる労務費を削減できます。
4-3. AI・ロボット導入による高付加価値化とコスト削減の両立
労務費率改善の最終的な目標は、単純作業をAIやロボットに任せることで、人がより価値の高い業務に集中できる体制を築くことです。
単純・反復作業の自動化
◦人手不足が深刻な中で、ロボットは単純作業を24時間体制で正確に実行できます。これにより、製品あたりの労務費を劇的に削減できます。
熟練技術者の高付加価値業務へのシフト
◦自動化により空いた時間を、技術者は新製品開発や品質改善、若手育成といったより創造的な業務に充てることが可能になります。これにより、企業の競争力と利益率を同時に高めることができます。
5. 【事例紹介】製造業DXで労務費率を改善した成功企業
ここでは、実際に製造業DXによって労務費率を改善した事例を、添付資料「リアルタイム現場データ可視化事例20選」を参考に紹介します。
5-1. ロボット導入で製造コストを削減した事例
ある企業では、製品製造における特定の工程に工数が集中し、製造コストが圧迫されているという課題を抱えていました。そこで、労務費の中でも大きな割合を占める「仕上げ工程」と「手直し」に着目し、その工数を削減するためのDXを推進しました。
添付画像の「工程別工数分析」の図表では、Worst3の製品は「仕上げ」工程がリードタイムの51%を占めているという課題が明確になりました。また、別の図表では、Worst1の製品は「手直し」が多いことが示されています。
この課題を解決するため、ロボットや自動機の導入による自動化を段階的に進めました。
自動化の成果
◦単純作業をロボットに任せることで、製造コストを大幅に削減しました。
◦また、添付資料の「設備別稼働状況管理」の図表にあるように、設備ごとの稼働状況がリアルタイムで可視化できるようになり、計画に対してどの程度作業が進んでいるかを正確に把握できるようになりました。
この事例は、単に人件費を削減するのではなく、ボトルネックとなっている工程を特定し、適切なデジタル技術を導入することで、労務費率を改善しつつ生産性を高めることが可能であることを示しています。
5-2. 生産管理システム導入で正確な原価を把握した事例
別の製造業の事例では、紙の日報によるデータ管理が原因で、製品ごとの正確な原価が把握できていないという課題がありました。特に、直接的な工賃だけでなく、間接費や手直し費をどこまで含めるべきか、という点で曖昧さが残っていました。
そこで、リアルタイムでデータを収集・分析できる生産管理システムを導入しました。
システム導入の成果
◦添付資料の「製品個別原価算出」の図表にあるように、製品ごとに実際にかかった原価構造や粗利が可視化されました。
◦「間接費を含めた原価管理」の図表にあるように、
工程別原価だけでなく、間接費や手直し費を含めた製品個別の実際原価管理が可能になりました。
◦ さらに、「製品別原価一覧」の表を用いることで、
製品ごとの粗利率を一覧で確認できるようになり、採算性の低い製品を特定し、営業戦略や製造計画に活かせるようになりました。
この事例は、正確な労務費データを取得・分析することが、企業の利益構造そのものを健全化させる上でいかに重要であるかを示しています。
参考レポート:「【製造業向け】リアルタイム現場データ可視化事例20選」
https://www.funaisoken.co.jp/dl-contents/smart-factory_smart-factory_03546_S045?media=smart-factory_S045
まとめ
この記事では、製造業の労務費率を改善するために、まず「労務費」を正しく理解し、その元となる「作業実績」データを正確に取得することの重要性について解説しました。紙の日報に代表されるアナログなデータ管理は、正確な経営判断を妨げる大きな課題です。
しかし、この課題は「製造業DX」によって解決できます。リアルタイムでのデータ可視化やAI・ロボットの活用は、単なるコスト削減を超え、企業の生産性向上と競争力強化に直結します。
利益率アップを実現するための第一歩は、労務費という指標に正面から向き合い、正確なデータを基にした「データの経営」へとシフトすることです。まずは自社の現状を分析し、小さなデジタルツールから導入を始めてみてはいかがでしょうか? はじめに
製造業の経営を考える上で、人件費は避けて通れないコストです。しかし、「社員の頑張りをコストと見なすのは忍びない」「人件費を削減すると、社員のモチベーションが下がってしまうのではないか」といった葛藤を抱えている経営者の方も少なくありません。
そこで重要になるのが、「労務費率」という指標です。この指標を正しく理解し、コントロールすることは、単なるコスト削減ではなく、企業の利益率を向上させ、競争力を高めることにつながります。この記事では、労務費率の基礎知識から、多くの企業が直面するデータ取得の課題、そしてそれを解決する「製造業DX」の具体的な手法まで、成功事例を交えて徹底的に解説します。
1. 利益率改善の鍵「労務費率」とは?製造業における重要性を再認識
製造業において、労務費率は経営の健康状態を測るための重要な羅針盤です。まずは、その基本的な定義と、なぜこれほどまでに注目すべき指標なのかを解説します。
1-1. そもそも「労務費」とは?人件費との違いを明確に理解する
労務費と人件費は混同されがちですが、会計上は明確に区別されます。
人件費 企業の従業員全体にかかる費用。給与や賃金、賞与、退職金、法定福利費(社会保険料など)のすべてを含みます。
労務費 人件費のうち、製品の製造に直接的・間接的に関わる人件費のみを指します。
つまり、工場で働く製造スタッフの給与は「労務費」に含まれますが、経理や営業、事務スタッフの給与は「労務費」には含まれず、「販売費及び一般管理費」として計上されます。
以下に、労務費と人件費の関係を図解で示します。
1-2. 製造業における「労務費率」の正しい計算方法
労務費率は、売上高に対する労務費の割合を示す指標です。製品の製造にかかる人件費が、売上に対してどれくらいの割合を占めているかを可視化できます。
労務費率(%) = 労務費 ÷ 売上高 × 100
この計算式を分解すると、労務費は「直接労務費」と「間接労務費」に分けることができます。
直接労務費: 特定の製品の製造に直接かかった賃金。例えば、組み立て作業員や加工技術者の賃金など。
間接労務費: 製造に間接的にかかった賃金。例えば、工場全体の管理者の給与や、特定の製品に関わらない清掃員の賃金など。
自社の労務費を正確に把握するためには、これらの内訳を細かく分類して管理することが不可欠です。
参考レポート:「【製造業 原価管理】時流予測レポート2025 (今後の見通し・業界動向・トレンド)」
https://www.funaisoken.co.jp/dl-contents/jy-cost_S045?media=smart-factory_S045
1-3. 労務費率はなぜ重要?経営者が注目すべき2つの理由
労務費率が経営にとって重要である理由は、主に以下の2つです。
製造原価の大部分を占めるため、コスト管理の要となる
◦製造原価は「材料費」「労務費」「経費」の3つで構成されます。多くの製造業では、この中で労務費が占める割合が非常に高く、労務費をコントロールすることが、製造原価全体の管理に直結します。
生産性の改善度合いを測る重要な指標となる
◦労務費率が高いということは、売上に対して人件費の負担が大きいことを意味します。これは、生産性が低い、つまり「同じ売上を上げるのに、より多くの人手と時間がかかっている」状態を示唆します。労務費率を改善することは、生産性を向上させることと同義です。
2. ほとんどの製造業が抱える課題:労務費のデータ取得が難しい理由
多くの経営者が労務費率の重要性を認識しているにもかかわらず、その改善に踏み切れない大きな壁があります。それは、労務費の元となる「作業実績」データの取得が難しいという現実です。
2-1. 「紙の日報」では正確な作業実績が把握できない現実
製造現場では、いまだに多くの企業が紙の日報に頼って作業実績を記録しています。しかし、このアナログな手法には、以下のような問題が潜んでいます。
手書きによる記録のばらつき:
◦作業者が「大体の時間」で記入するため、実際の作業時間との間に乖離が生じやすいです。
◦「加工」「組み立て」といった大まかなカテゴリでしか記録されず、具体的な作業内容や、何にどれだけの時間がかかったのかが不明瞭になります。
これにより、日報のデータは現場の正確な状況を反映しない「不正確なデータ」となり、その後の経営判断を誤らせる原因となります。
2-2. データが不正確だと「見積もりと実際の利益」が一致しない
不正確な労務費データは、深刻な経営課題を引き起こします。
製品ごとの採算性が不明瞭になる:
◦紙の日報では、製品ごとの正確な作業時間がわからないため、個別の原価を算出することが困難です。結果として、見積もり段階では利益が出るはずだったのに、実際には赤字になっていた、という事態が起こりえます。
「勘と経験」に頼った経営から抜け出せない:
◦正確なデータがないため、「この製品は利益が出ているはず」「この作業はムダが多い」といった感覚的な判断に頼らざるを得ません。これでは、科学的な根拠に基づいた経営改善は不可能です。
3. 労務費率を改善する前に!避けるべき「コスト削減のワナ」
労務費率の改善と聞いて、まず「人件費を減らす」「残業をなくす」といった安易なコストカットを思い浮かべる方もいるかもしれません。しかし、これらはかえって企業に大きなダメージを与える可能性があります。
3-1. 安易な人件費削減は生産性低下を招く
給与の引き下げや人員整理は、一時的な労務費率の改善にはなるかもしれません。しかし、長期的に見れば、社員のモチベーション低下や技術力の流出を招き、結果的に生産性を大きく低下させます。特に熟練技術者の流出は、企業の競争力そのものを失わせる危険性があります。
3-2. 設備投資は「利益率向上」に繋がるか?費用対効果の見極め方
「労務費削減のために最新の機械を導入しよう」と考えることもあるでしょう。しかし、その投資が本当に利益率向上につながるかは慎重な見極めが必要です。多額の設備投資を行ったにもかかわらず、稼働率が上がらず、新たなコスト負担だけが増えてしまう失敗例も少なくありません。重要なのは、投資が「現場のボトルネック解消」や「高付加価値化」にどう貢献するかを明確にすることです。
4. 利益率を最大化する「製造業DX」による労務費率改善の具体策
前述の課題を解決し、労務費率を根本から改善するために最も効果的なのが「製造業DX」です。ここでは、DXがもたらす革新的な改善策を具体的に解説します。
4-1. リアルタイムデータ可視化による正確な工数管理
最も効果的なのは、現場の作業をリアルタイムでデータ化し、正確な工数を把握することです。IoTセンサーやデジタル日報システムを導入することで、以下のことが可能になります。
正確な稼働時間の記録:
◦機械の稼働状況や作業者の動きを自動で記録し、手書き日報で発生する「勘」や「ばらつき」を排除します。
作業内容の見える化:
◦どの製品のどの工程に、どれだけの時間がかかっているかを正確に把握できます。これにより、見積もり段階での工数と実績を比較し、精度の高い原価管理が可能になります。
4-2. データの見える化で「ムダ」を発見し、生産性を向上させる
リアルタイムで収集したデータは、単なる記録ではありません。分析することで、現場に潜む様々な「ムダ」を発見し、生産性向上に直結する知見を得られます。
生産ラインのボトルネック特定:
◦データにより、特定の工程で作業が滞っている「ボトルネック」を可視化できます。
不良率の根本原因分析:
◦いつ、どの工程で、どのような不良が発生しているかをデータで追跡することで、不良の原因を特定し、対策を講じることができます。これにより、手直しや廃棄にかかる労務費を削減できます。
4-3. AI・ロボット導入による高付加価値化とコスト削減の両立
労務費率改善の最終的な目標は、単純作業をAIやロボットに任せることで、人がより価値の高い業務に集中できる体制を築くことです。
単純・反復作業の自動化
◦人手不足が深刻な中で、ロボットは単純作業を24時間体制で正確に実行できます。これにより、製品あたりの労務費を劇的に削減できます。
熟練技術者の高付加価値業務へのシフト
◦自動化により空いた時間を、技術者は新製品開発や品質改善、若手育成といったより創造的な業務に充てることが可能になります。これにより、企業の競争力と利益率を同時に高めることができます。
5. 【事例紹介】製造業DXで労務費率を改善した成功企業
ここでは、実際に製造業DXによって労務費率を改善した事例を、添付資料「リアルタイム現場データ可視化事例20選」を参考に紹介します。
5-1. ロボット導入で製造コストを削減した事例
ある企業では、製品製造における特定の工程に工数が集中し、製造コストが圧迫されているという課題を抱えていました。そこで、労務費の中でも大きな割合を占める「仕上げ工程」と「手直し」に着目し、その工数を削減するためのDXを推進しました。
添付画像の「工程別工数分析」の図表では、Worst3の製品は「仕上げ」工程がリードタイムの51%を占めているという課題が明確になりました。また、別の図表では、Worst1の製品は「手直し」が多いことが示されています。
この課題を解決するため、ロボットや自動機の導入による自動化を段階的に進めました。
自動化の成果
◦単純作業をロボットに任せることで、製造コストを大幅に削減しました。
◦また、添付資料の「設備別稼働状況管理」の図表にあるように、設備ごとの稼働状況がリアルタイムで可視化できるようになり、計画に対してどの程度作業が進んでいるかを正確に把握できるようになりました。
この事例は、単に人件費を削減するのではなく、ボトルネックとなっている工程を特定し、適切なデジタル技術を導入することで、労務費率を改善しつつ生産性を高めることが可能であることを示しています。
5-2. 生産管理システム導入で正確な原価を把握した事例
別の製造業の事例では、紙の日報によるデータ管理が原因で、製品ごとの正確な原価が把握できていないという課題がありました。特に、直接的な工賃だけでなく、間接費や手直し費をどこまで含めるべきか、という点で曖昧さが残っていました。
そこで、リアルタイムでデータを収集・分析できる生産管理システムを導入しました。
システム導入の成果
◦添付資料の「製品個別原価算出」の図表にあるように、製品ごとに実際にかかった原価構造や粗利が可視化されました。
◦「間接費を含めた原価管理」の図表にあるように、
工程別原価だけでなく、間接費や手直し費を含めた製品個別の実際原価管理が可能になりました。
◦ さらに、「製品別原価一覧」の表を用いることで、
製品ごとの粗利率を一覧で確認できるようになり、採算性の低い製品を特定し、営業戦略や製造計画に活かせるようになりました。
この事例は、正確な労務費データを取得・分析することが、企業の利益構造そのものを健全化させる上でいかに重要であるかを示しています。
参考レポート:「【製造業向け】リアルタイム現場データ可視化事例20選」
https://www.funaisoken.co.jp/dl-contents/smart-factory_smart-factory_03546_S045?media=smart-factory_S045
まとめ
この記事では、製造業の労務費率を改善するために、まず「労務費」を正しく理解し、その元となる「作業実績」データを正確に取得することの重要性について解説しました。紙の日報に代表されるアナログなデータ管理は、正確な経営判断を妨げる大きな課題です。
しかし、この課題は「製造業DX」によって解決できます。リアルタイムでのデータ可視化やAI・ロボットの活用は、単なるコスト削減を超え、企業の生産性向上と競争力強化に直結します。
利益率アップを実現するための第一歩は、労務費という指標に正面から向き合い、正確なデータを基にした「データの経営」へとシフトすることです。まずは自社の現状を分析し、小さなデジタルツールから導入を始めてみてはいかがでしょうか?