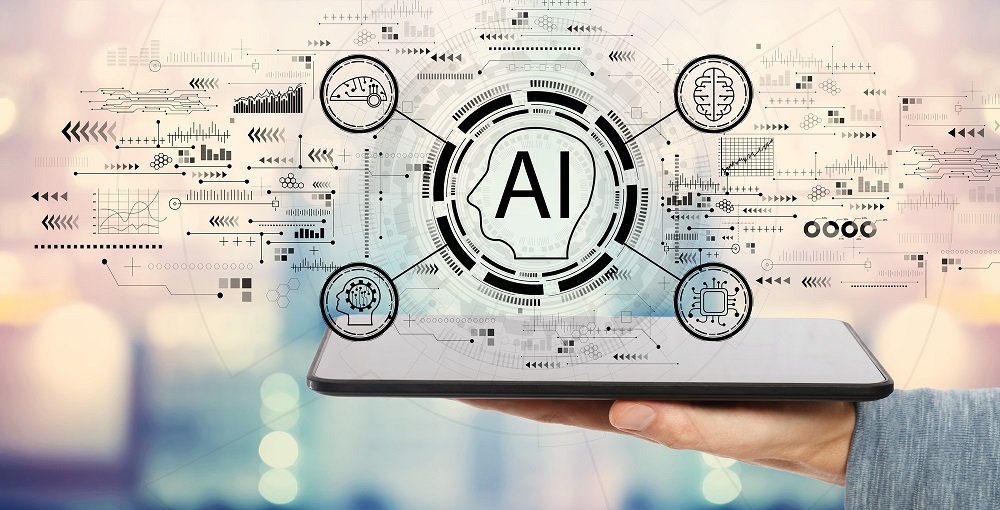
生成AIの上手な使い方
2023.08.24
1.生成AIとは何か?生成AIのインパクト
今、話題の生成AIですが、我々の身の回りはすでに生成AIで作られたものでとり囲まれているかもしれません。
インターネットで目にする文章、画像、音声などは実は今、私たちが知らないうちに大量にAIで作られています。
生成AIとは、簡単にいうと、「様々なコンテンツを自動で大量に生成できるAI」のことを指します。
従来の「AI」と「生成AI」の違いについては、「オリジナルコンテンツ創造の可否」にあります。
従来AIは「学習済みのデータの中から適切な回答を探して提示する性質」を持っていましたが、生成AIは「0から1を生み出す性質(オリジナルコンテンツを創出)」が特徴です。
AIが、作家が作ったような文章を書き、芸術家が描くような画像を生成してくれます。
生成AIは人間の仕事や作業をサポートしてくれる(短時間で生成する)ツールとして急速に注目を集め、利用されています。
2.AIはやる/やらないではなく、来るもの
よく社内で「AIを活用するか、しないか」を議論されているという話聞きます。
これは、インターネット到来時代に「インターネットを使うか、使わないか」を議論していることと同じです。
人間は便利なものは必ず使うようになります。
「スマホよりガラケーの方がいい」と言っていた方々も、今は全員スマホを使っています。
人間は利便性がよい方に確実に転がります。
「AIは使えない!」という方々も良くいますが、それはAI自体をよく知らないか、使い方を間違えている方々です。
<ハサミで金棒は切れません>
AIが使えないという方々は「ハサミで金棒を切って、使えない」と言っているに過ぎません。
AIは万能ではありません。
使い方があり、使えないというのは、そもそも使い方を理解していないのです。
AIを正しく理解して、正しく使えば、便利なものには間違いありません。
ただ、業務利用するにはきちんとした知識が必要です。
知識もないまま、AIを扱うと間違いなく痛い目に遭うでしょう。
3.AIと仲良く暮らすには?
私たちは誰もかれも「現状が好きな生き物」です。
携帯電話が到来した時、「家に電話すれば済む。用事があれば公衆電話があるし、出掛けているときに捕まりたくない」と私たちは思っていました。
インターネットが到来した時も、「やっぱり紙がいい。パソコンは難しい・わかりづらい」と私たちは思っていました。
スマホが到来した時も、「ガラケーで十分。スマホはわかりづらい」と私たちは思っていました。
新しいものが出てきた時に、私たちは必ず「今のままで良い」と思うのです。
ただ、手のひら返しをするタイミングは思いのほかすぐにやってくるのです。
AIがわからないという方は、とりあえずchat-GPTサービスをまずは試してください。
もしかしたら、「役に立たない。
インターネットで検索すれば十分」と思うかもしれません。
それでもいろいろなことを試して見てください。
いろいろな可能性が見えるかもしれません。
すでに身近にAIサービスは見えるもの・見えないものたくさんリリースされています。
現状のAI技術にたくさん触れて、今のAIのレベルを確認してください。
幸いAIの進化はとても早く、1年も経てば、別の世界を見せてくれます。
頑張って、抗っても、拒絶してもAIの時代はやってきます。
事実、すでに身の回りの文章や画像が、人が作ったのか、AIが作ったのか、誰にもわかりません。
この文章自体、AIが書いているかもしれません。
確実なことは「AIが便利なものであること」「どの会社も人材不足」ということです。
この技術を皆さんのビジネスにどう有意義に生かしてくか、ただそれだけなのだと思います。
最後までお読みいただきありがとうございました。
製造業経営者向け“基幹システム再構築戦略”解説レポート
▼事例レポート無料ダウンロードお申し込みはこちら▼
多くの製造業は、全体としての原価・利益は見えているが、個別の実際原価は、属人化している業務で運用されている事で見えにくくなっています。製品別個別、取引先個別、工程別個別の実際原価を把握することで実際の利益が見えてきます。
見える化、DX化により、適切なアクションを取ることが重要です。
本レポートでは見える化とDX化のポイントを解説します!
https://www.funaisoken.co.jp/dl-contents/smart-factory__02003_S045
■関連するセミナーのご案内
製造業の為のAI・IoT活用戦略!経営者セミナー
https://www.funaisoken.co.jp/seminar/102603
職人技術に依存している製造現場でAI化・IoT化・ロボット化・デジタル化できる取組事例が学べる!
■開催日程
全てオンライン開催となります
以下の日程よりご都合の良い日程をお選び下さい
※内容は全て一緒です
2023/09/07 (木) 13:00~15:00
2023/09/12 (火) 13:00~15:00
2023/09/14 (木) 13:00~15:00
■講座内容
ゲスト講師講座「協働ロボット成功事例講座!ロボドリル工程の工数を年間1,200時間削減!」
AI・IoT取組事例講座編 「全国各地で見られる製造業でのAI・IoT取組事例」
AI・IoT活用戦略講座編 「製造業経営者が取り組むべきAI・IoT活用戦略」
セミナー詳細・申込はこちらから⇒
https://www.funaisoken.co.jp/seminar/102603 いつも当コラムをご愛読いただきありがとうございます。
1.生成AIとは何か?生成AIのインパクト
今、話題の生成AIですが、我々の身の回りはすでに生成AIで作られたものでとり囲まれているかもしれません。
インターネットで目にする文章、画像、音声などは実は今、私たちが知らないうちに大量にAIで作られています。
生成AIとは、簡単にいうと、「様々なコンテンツを自動で大量に生成できるAI」のことを指します。
従来の「AI」と「生成AI」の違いについては、「オリジナルコンテンツ創造の可否」にあります。
従来AIは「学習済みのデータの中から適切な回答を探して提示する性質」を持っていましたが、生成AIは「0から1を生み出す性質(オリジナルコンテンツを創出)」が特徴です。
AIが、作家が作ったような文章を書き、芸術家が描くような画像を生成してくれます。
生成AIは人間の仕事や作業をサポートしてくれる(短時間で生成する)ツールとして急速に注目を集め、利用されています。
2.AIはやる/やらないではなく、来るもの
よく社内で「AIを活用するか、しないか」を議論されているという話聞きます。
これは、インターネット到来時代に「インターネットを使うか、使わないか」を議論していることと同じです。
人間は便利なものは必ず使うようになります。
「スマホよりガラケーの方がいい」と言っていた方々も、今は全員スマホを使っています。
人間は利便性がよい方に確実に転がります。
「AIは使えない!」という方々も良くいますが、それはAI自体をよく知らないか、使い方を間違えている方々です。
<ハサミで金棒は切れません>
AIが使えないという方々は「ハサミで金棒を切って、使えない」と言っているに過ぎません。
AIは万能ではありません。
使い方があり、使えないというのは、そもそも使い方を理解していないのです。
AIを正しく理解して、正しく使えば、便利なものには間違いありません。
ただ、業務利用するにはきちんとした知識が必要です。
知識もないまま、AIを扱うと間違いなく痛い目に遭うでしょう。
3.AIと仲良く暮らすには?
私たちは誰もかれも「現状が好きな生き物」です。
携帯電話が到来した時、「家に電話すれば済む。用事があれば公衆電話があるし、出掛けているときに捕まりたくない」と私たちは思っていました。
インターネットが到来した時も、「やっぱり紙がいい。パソコンは難しい・わかりづらい」と私たちは思っていました。
スマホが到来した時も、「ガラケーで十分。スマホはわかりづらい」と私たちは思っていました。
新しいものが出てきた時に、私たちは必ず「今のままで良い」と思うのです。
ただ、手のひら返しをするタイミングは思いのほかすぐにやってくるのです。
AIがわからないという方は、とりあえずchat-GPTサービスをまずは試してください。
もしかしたら、「役に立たない。
インターネットで検索すれば十分」と思うかもしれません。
それでもいろいろなことを試して見てください。
いろいろな可能性が見えるかもしれません。
すでに身近にAIサービスは見えるもの・見えないものたくさんリリースされています。
現状のAI技術にたくさん触れて、今のAIのレベルを確認してください。
幸いAIの進化はとても早く、1年も経てば、別の世界を見せてくれます。
頑張って、抗っても、拒絶してもAIの時代はやってきます。
事実、すでに身の回りの文章や画像が、人が作ったのか、AIが作ったのか、誰にもわかりません。
この文章自体、AIが書いているかもしれません。
確実なことは「AIが便利なものであること」「どの会社も人材不足」ということです。
この技術を皆さんのビジネスにどう有意義に生かしてくか、ただそれだけなのだと思います。
最後までお読みいただきありがとうございました。
製造業経営者向け“基幹システム再構築戦略”解説レポート
▼事例レポート無料ダウンロードお申し込みはこちら▼
多くの製造業は、全体としての原価・利益は見えているが、個別の実際原価は、属人化している業務で運用されている事で見えにくくなっています。製品別個別、取引先個別、工程別個別の実際原価を把握することで実際の利益が見えてきます。
見える化、DX化により、適切なアクションを取ることが重要です。
本レポートでは見える化とDX化のポイントを解説します!
https://www.funaisoken.co.jp/dl-contents/smart-factory__02003_S045
■関連するセミナーのご案内
製造業の為のAI・IoT活用戦略!経営者セミナー
https://www.funaisoken.co.jp/seminar/102603
職人技術に依存している製造現場でAI化・IoT化・ロボット化・デジタル化できる取組事例が学べる!
■開催日程
全てオンライン開催となります
以下の日程よりご都合の良い日程をお選び下さい
※内容は全て一緒です
2023/09/07 (木) 13:00~15:00
2023/09/12 (火) 13:00~15:00
2023/09/14 (木) 13:00~15:00
■講座内容
ゲスト講師講座「協働ロボット成功事例講座!ロボドリル工程の工数を年間1,200時間削減!」
AI・IoT取組事例講座編 「全国各地で見られる製造業でのAI・IoT取組事例」
AI・IoT活用戦略講座編 「製造業経営者が取り組むべきAI・IoT活用戦略」
セミナー詳細・申込はこちらから⇒
https://www.funaisoken.co.jp/seminar/102603