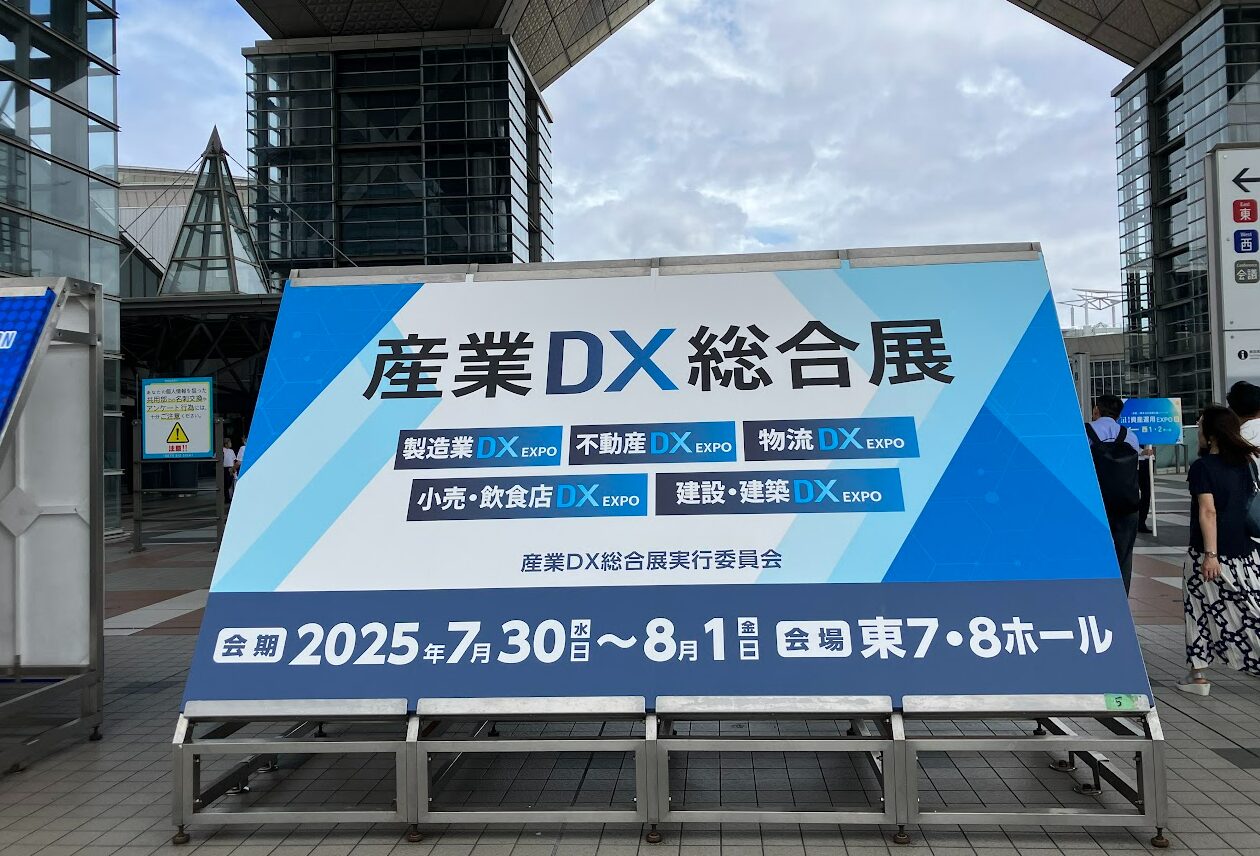
【事例紹介】製造業DX EXPO2025に行ってきました
2025.08.05
URL: https://www.funaisoken.co.jp/dl-contents/jy-cost_S045
1. 株式会社システム計画研究所様
株式会社システム計画研究所様では、AIカメラを活用した作業動作解析システムを紹介していました。
工程や作業場所にAIカメラを設置することで、作業者が作業場所にいるかいないか、何の作業をしているかを判別し、可視化するシステムです。
これを作業指示書や、設備稼働データと連携することで、紙日報よりも、正確な作業実績データを取得することができます。
2. SOLIZE Ureka Technology株式会社様
SOLIZE Ureka Technology株式会社様では、ベテランや職人の暗黙知を形式知化するAIを開発していました。
多くの製造業ではベテランの暗黙知を引き継ぐのが難しく、品質の低下が課題となっていますが、ベテランの思考の中身を分析していくと、40%が作業、50%が選択的判断、残りの10%がベテランならではの判断と言う分析結果が出ているとのことです。そのためAIでは10%のベテランならではの判断に着目し、設計業務の業務効率化に大きく貢献できるようになります。
3. デジタル・インフォメーション・テクノロジー株式会社
デジタル・インフォメーション・テクノロジー株式会社では、日々のExcel業務の自動化を開発していました。
主に明細からの集計表作成やグラフ表作成、CSVの作成など工数のかかる業務を自動化できます。
まずは既存のExcelで自動化させる処理内容のルールを作り、作業手順のシナリオを作成します。そこからウェブアプリの設定を行うと1クリックで業務を実行できるようになります。
また、異なるフォーマットの集計や、分類の差分、抽出、システム間連携用データ、フォーマット整形、RPA連携ができます。
これにより、請求書発行業務が月180時間削減された事例や、データ集計工数が年間7000時間削減された事例がありました。
4. Tebiki株式会社
Tebiki株式会社では、製造業の現場の作業マニュアルを動画で作成するツールを開発していました。
マニュアル作成にはスマホの撮影で動画を作成し、100カ国以上の言語に翻訳ができます。また複数の動画を1つのコースにまとめることで、手順をステップ化することができます。
海外からの作業研修生が多い製造業において、作業の標準化やマニュアル化は大きな課題となっておりマニュアル作成と翻訳機能は重要になります。
5. まとめ
以上がピックアップした事例企業になります。
その他にも、図面管理やバックオフィスの効率化など多くのシステム出展していました。
今後も情報発信を進めていきますのでご期待下さい。
URL: https://www.funaisoken.co.jp/dl-contents/smart-factory__00000426_S045
URL:https://lp.funaisoken.co.jp/mt/form01/inquiry-S045.html?siteno=S045 URL: https://www.funaisoken.co.jp/dl-contents/jy-cost_S045
1. 株式会社システム計画研究所様
株式会社システム計画研究所様では、AIカメラを活用した作業動作解析システムを紹介していました。
工程や作業場所にAIカメラを設置することで、作業者が作業場所にいるかいないか、何の作業をしているかを判別し、可視化するシステムです。
これを作業指示書や、設備稼働データと連携することで、紙日報よりも、正確な作業実績データを取得することができます。
2. SOLIZE Ureka Technology株式会社様
SOLIZE Ureka Technology株式会社様では、ベテランや職人の暗黙知を形式知化するAIを開発していました。
多くの製造業ではベテランの暗黙知を引き継ぐのが難しく、品質の低下が課題となっていますが、ベテランの思考の中身を分析していくと、40%が作業、50%が選択的判断、残りの10%がベテランならではの判断と言う分析結果が出ているとのことです。そのためAIでは10%のベテランならではの判断に着目し、設計業務の業務効率化に大きく貢献できるようになります。
3. デジタル・インフォメーション・テクノロジー株式会社
デジタル・インフォメーション・テクノロジー株式会社では、日々のExcel業務の自動化を開発していました。
主に明細からの集計表作成やグラフ表作成、CSVの作成など工数のかかる業務を自動化できます。
まずは既存のExcelで自動化させる処理内容のルールを作り、作業手順のシナリオを作成します。そこからウェブアプリの設定を行うと1クリックで業務を実行できるようになります。
また、異なるフォーマットの集計や、分類の差分、抽出、システム間連携用データ、フォーマット整形、RPA連携ができます。
これにより、請求書発行業務が月180時間削減された事例や、データ集計工数が年間7000時間削減された事例がありました。
4. Tebiki株式会社
Tebiki株式会社では、製造業の現場の作業マニュアルを動画で作成するツールを開発していました。
マニュアル作成にはスマホの撮影で動画を作成し、100カ国以上の言語に翻訳ができます。また複数の動画を1つのコースにまとめることで、手順をステップ化することができます。
海外からの作業研修生が多い製造業において、作業の標準化やマニュアル化は大きな課題となっておりマニュアル作成と翻訳機能は重要になります。
5. まとめ
以上がピックアップした事例企業になります。
その他にも、図面管理やバックオフィスの効率化など多くのシステム出展していました。
今後も情報発信を進めていきますのでご期待下さい。
URL: https://www.funaisoken.co.jp/dl-contents/smart-factory__00000426_S045
URL:https://lp.funaisoken.co.jp/mt/form01/inquiry-S045.html?siteno=S045