記事公開日:2020.02.28
最終更新日:2023.08.19
溶接ロボットシステムの構成と使用方法
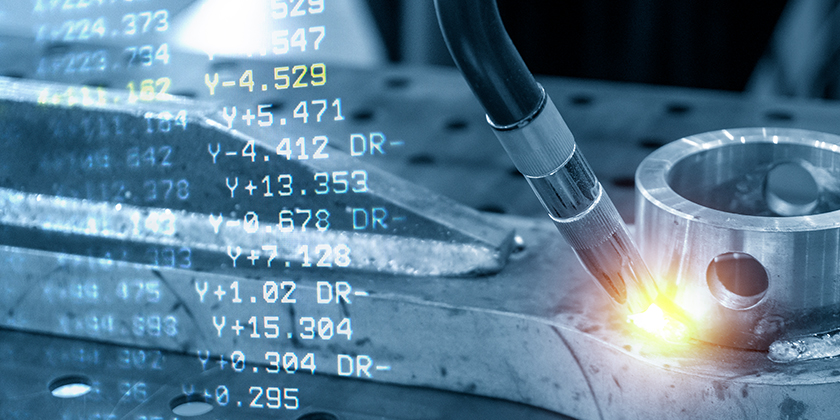
一般的に産業用ロボットによる自動溶接にはガスシールドアーク溶接を用います。
ガスシールドアーク溶接とは、溶接による接合部に不活性ガスを吹き付けながら接合し、接合部の変色や錆を防止するものです。不活性ガスにてアーク発生部の周囲をシールド(保護)する溶接方法を下記に分類していきます。
目次
ガスシールドアーク溶接の分類と使い分けについて
ガスシールドアーク溶接は,
1、消耗電極式
2、非消耗電極式
に大別されます。
・消耗電極式にはシールドガスの種類によって分類されます
1、MIG(Metal Inert Gas)溶接
ミグ溶接はAr,He(または,これらの混合ガス)のような不活性ガス,あるいは,これに酸素や炭素ガスのような活性ガスを少量添加してシールドガスとして用いる方法
2、MAG(Metal Active Gas)溶接
①炭酸ガスアーク溶接(シールドガスとして炭酸ガスを用いるもの)
②混合ガスアーク溶接(シールドガスとしてアルゴンと炭酸ガスの混合ガスを用いる)
・非消耗電極式のガスシールドアーク溶接
3、TIG(Tungsten Inert Gas)溶接(アルゴン雰囲気中でタングステン電極と母材との間にアークを発生させ,そのアーク熱によって溶加材および母材を溶融して溶接する方法)
それぞれの溶接方法の特徴
(1) マグ溶接(MAG溶接)
マグ溶接は安価な炭酸ガスを単独で,またはアルゴンと混合して用いる溶接方法で軟鋼,高張力鋼,および低合金鋼の溶接に広く用いられています。マグ溶接に用いられるソリッドワイヤやフラックス入りワイヤは,自動化が安易で溶接の合理化が図りやすいため,全溶接材料の中に占める使用比率は近年非常に高くなっています。
(2) ミグ溶接(MIG溶接)
ミグ溶接はアルミニウム,チタンのように本来は溶接時に酸化,窒化しやすい金属を対象に開発され,その他非鉄金属,ステンレス鋼等にも使用されていた。純イナートガスでシールドしながら溶接する場合と,ステンレス鋼の場合のようにアーク安定性の面より若干の酸素を混合して使用する場合があります。ミグ溶接によれば清浄な溶着金属が得られますが,アルゴンが高価なため適用される範囲はアルミニウム合金,ステンレス鋼,耐熱合金鋼等が主体です。
(3) ティグ溶接(TIG溶接)
溶接トーチと溶加棒とをそれぞれ手で持って行う溶接が主ですが,溶接ワイヤを自動的に送給してトーチも自動送りする全自動ティグ溶接装置も実用化されており,溶接ロボットにティグ溶接を適用している例もあります。
ティグ溶接は非消耗電極式であるためワイヤ自身が電極となってアーク熱で溶融する消耗電極式と異なり,電極からの溶融金属の移行がないので,これによるアーク不安定さやスパッタの発生がなく静かな溶接法です。
ロボット化が進んでいる製造現場
ロボットは工場で加工する溶接作業に多く用いられています。
特に自動車は,溶接個所が多く,同じ物が繰り返し生産されるので,ロボット化が容易に行えます。溶接方法としては、SPOT溶接が特に進んでいます。ロボット溶接によって自動車部品の溶接個所で品質の安定と大量生産が可能になりました。
他には事務機器・農機具・家電・車両など工場内溶接で量産品がある場合は,溶接物の材質(鋼材・ステンレス材・アルミニウム材)や板厚に関係なく,また企業の規模に関係なくロボット化が進んでいます。
一方,造船や橋梁・建設も溶接は多いですが,現場溶接が多いことと溶接部位が多種多様にわたるため一部を除いてロボット化は進んでおりません。
溶接ロボットシステムの構成
アーク溶接ロボットの標準的な構成は下記があります。対象となるワークや工法に応じて最適なシステム選定が必要です。
①マニピュレータ(ロボット本体)
②制御装置(コントローラ)
③ティーチペンダント
④溶接電源
⑤溶接トーチ(MIG,MAG、TIG溶接方法に合ったもの)
⑥ワイヤ供給装置(溶接方法に合ったもの)
⑦回転テーブル(小物、複雑形状物対象)
様々な角度で最適な溶接を実現する為に、多関節ロボット+回転テーブルでの自動化システムが昨今では標準になってきています。
回転テーブルとは、単軸、複数軸を持ち、溶接するワークを固定しながら、任意の角度にテーブルが回転し、様々な形状のワークに対しても効率的なロボット溶接を可能にしてくれるテーブルです。軸数や可搬重量もさまざまラインナップがあり、複雑な形状のワークや指定された加工条件を満たすための溶接方法の実現を助けてくれます。またロボットコントローラーと連動して動かす事が出来るので、ティーチングも比較的簡単になってきています。
溶接ロボットの使用方法
溶接ロボットを使用する為には手順を正確に行う必要があります。ロボットを導入すればすぐに良い品質のモノが出来るわけではありません。地道に一つ一つの作業にて発生する課題をクリアしていく事で、最終的な品質を担保していくことができます。
①溶接ワークの固定治具設計
(接合物やワークを固定する治具の設計)
②ロボットのティーチング
(溶接トーチの軌道や溶接開始点、終了点の教示)
③溶接条件の見直し
(溶接状況や仕上がりを確認しながら、溶接電流やトーチの向き、角度の調整)
④自動運転
(実際に自動運転をしてさらに高品質なモノが生産できるように調整を重ねていく)
溶接方法やワーク形状によっては、トーチがワークに届かない、うまく接合が出来ないなど発生します。課題が発生した時は、治具の設計を見直し、溶接トーチの大きさや角度を調整する必要があります。
ロボットは、良くも悪くも融通が利きませんので、人任せに行っていた作業を自動化する際は必ず作業の要素分解と技術的な解決策が必要です。
ロボットティーチング(教示)について
基本的には、各社ロボットメーカーの標準ソフトウェアとティーチングペンダントを使用してロボットにティーチングを行います。ティーチングペンダントによるロボットの操作は各社メーカーが行う教育を受ければ、数日で動作させる事が可能です。(一般的にロボットメーカーで2日間程度の講習会を開催しています。)
しかし、ペンダントによる操作が出来るようになっても、実際に溶接が品質水準を満たすものに仕上げるために、何度も試運転と調整が必要です。溶接に対する知識を持っている方のアドバイスも必要になってくるでしょう。
ロボットメーカー以外にも、CAD上で溶接の軌道を自動でシュミレーションしてロボットPRGを作成してくれるオフラインティーチングソフトウェアを販売している会社も数社あります。非常に便利なソフトウェアが開発されており、ライセンス制で価格も数百万しますが、ティーチングの頻度や難易度を検討した上で購入される企業も多いようです。
そして、安全面については特に注意し、ロボット作業に従事する人は,労働安全衛生法で「産業用ロボットに関する安全衛生特別教育」の受講が義務づけられていますので必ず受講してからの作業が必須となります。この資格はロボットメーカーで行われる操作講習会に参加することで得られます。
まとめ
今回は溶接の種類やロボット溶接の方法について述べて来ました。もともと人が行ってきた作業を自動化するのは、要件定義ができれば難しいことではありません。一番大事なのは、導入のコストや自動化システムの継続的な活用(品種追加や溶接条件変更への対応)です。
溶接工が不足すると想定される溶接業界のロボット塗装の取り組みは、今後も加速していくと考えられますが、自在にロボットを操れる人材が少ないのも現状です。
すでにロボット塗装を導入されている企業は、比較的若手社員にロボットを自在に操る教育に力を入れています。ロボット操作者の教育と確保が今後溶接業全体の主流になりそうだと感じます。
(参考文献 一般社団法人 日本溶接協会HP http://www-it.jwes.or.jp/qa/index.jsp )
工場のロボット活用に関するおすすめ記事
・産業用ロボットの価格はどれくらい?工場への導入までの流れとコストを解説
溶接ロボットに関するおすすめ記事
・溶接の自動化・ロボット化とは?溶接の種類と自動化のポイントを解説
・ロボット溶接システムの品質と稼働を安定させる為の自動補正機能とは?(溶接線の自動補正を可能にするセンサーの機能や役割を解説)