記事公開日:2023.10.31
最終更新日:2023.10.31
“現場が使える基幹システム”導入成功事例とは?- 静岡県の食品加工業のケーススタディ
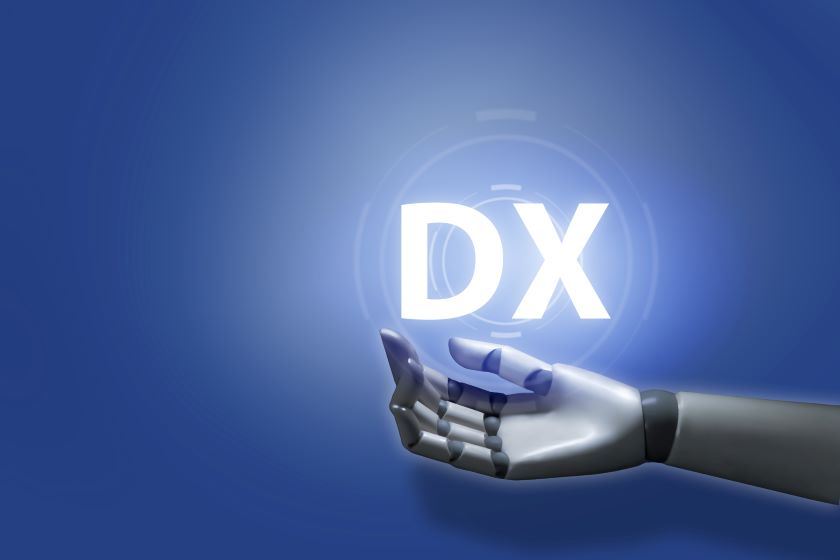
いつも当コラムをご愛読いただきありがとうございます。
“今回は、「“現場が使える基幹システム”導入成功事例とは?」と題して、お伝えさせていただきます。
1.成功事例の概要
- 本社:静岡県
- 従業員数規模:100名台
- 主な業種:食品加工、食品用包材の成形加工・包装加工等
- 基幹システムの導入を通じて、「歩留まり集計の自動化・リアルタイム化」等を実現
2.基幹システム導入のBefore/After
【Before(システム導入前の状態と主な課題)】
- 扱う食品の標準原価が曖昧だった(扱う食品の流動的な歩留まりを掴むことが難しかった)
- 個別原価計算を実施しておらず、製品個別の原価を把握できていなかった
- Excel等の手入力や二重三重入力が常態化していた
- アナログ中心の生産管理体制であるがゆえに、業務自体が職人化・属人化していた
- 在庫管理の体制も不十分なため、戦略的な値決めができていなかった
【After(システム導入後の主な効果】
煩雑かつアナログな歩留まり管理に悩まされていた中、
生産管理・原価管理システムの導入を通じて、
- 歩留まり集計の自動化・リアルタイム化
- 迅速な値決め&適正な値決めによる収益アップ
- 棚卸時間50%削減(毎月実施⇒隔月実施へ半減)
を実現!
その他にもシステム導入を通じて、
- データの一元化により、「生産部と管理部のリモート連携」を実現!
- 「生産・出荷した商品のトレース管理」も楽々実現!
- 「不透明かつ不正確な在庫・原価」をすべて可視化!
- システムへ蓄積したデータを分析し、販売戦略の立案・実行を推進!
成功のポイントとは?
3.基幹システム導入 成功のポイント
①導入するシステムに合わせて「既存のアナログ業務」の見直し・改善を実行!
⇒「既存のアナログ業務」をそのまま残すのではなく、
システム導入をきっかけとしてあらゆるムダな業務や手間のかかる業務を削減。
また、扱う商品の「構成部品設定方法」にも改めて見直しをかけることで、より円滑にシステム導入を進めるための土台を作った。
②受発注・原価・在庫・商品トレース等の情報をすべてシステムで一元管理!
⇒クラウド型のシステムを導入することで、
パソコンやタブレット端末が使える環境であれば、場所を問わずにいつでもリアルタイムでシステムを使用することが可能に。
1つのシステムにあらゆる業務情報を集約することで、「現場が使えるシステム」を実現した。
③間接業務を削減することで、「歩留まり改善・収益改善に向けた思考・分析時間」を確保!
⇒紙とExcelを駆使した「アナログな手集計や手作業の時間」を大幅に低減することができた。
と同時に、従来は間接業務に割いていた時間を「業績アップのための思考時間」へ充てることが可能に。
導入したシステムに集約・蓄積したデータを分析することで、その後の歩留まり改善・値決めの適正化へと繋げていくことができた。
製造業経営者向けIoTを活用した原価データ取得事例解説レポート
- 中小製造業が実践すべき製造工程でのIoT活用
- 具体的な取り組み方
- IoTを活用した 工数(労務原価)データ取得事例
https://www.funaisoken.co.jp/dl-contents/smart-factory_smart-factory_02162_S045
■関連するセミナーのご案内
特注・一品一様生産 機械加工業の為の見積AI 経営セミナー
特注生産・一品一様生産における属人的な見積業務にAI導入して受注率UP&利益率UP!
セミナー詳細・申込はこちらから
https://www.funaisoken.co.jp/seminar/105866
■開催日程
オンラインでの開催です
以下の日程よりご都合の良い日程をお選び下さい
※内容は全て一緒です
- 2023/11/20 (月) 13:00~15:00
- 2023/11/24 (金) 13:00~15:00
- 2023/11/28 (火) 13:00~15:00
お申し込みはこちらから⇒
https://www.funaisoken.co.jp/seminar/105149
関連コラム
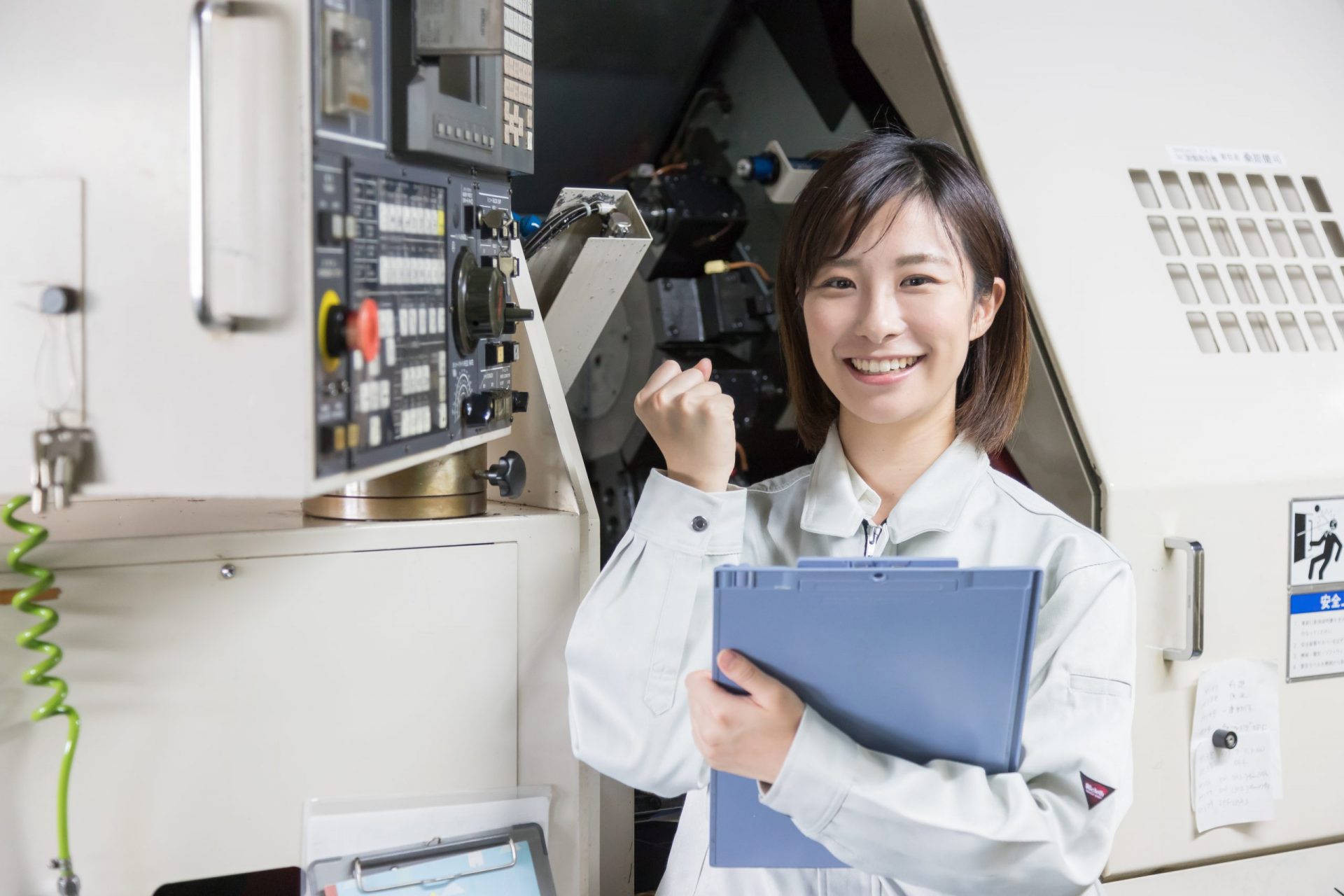
多品種少量生産ロボット導入における人材育成とは?
2020.11.13
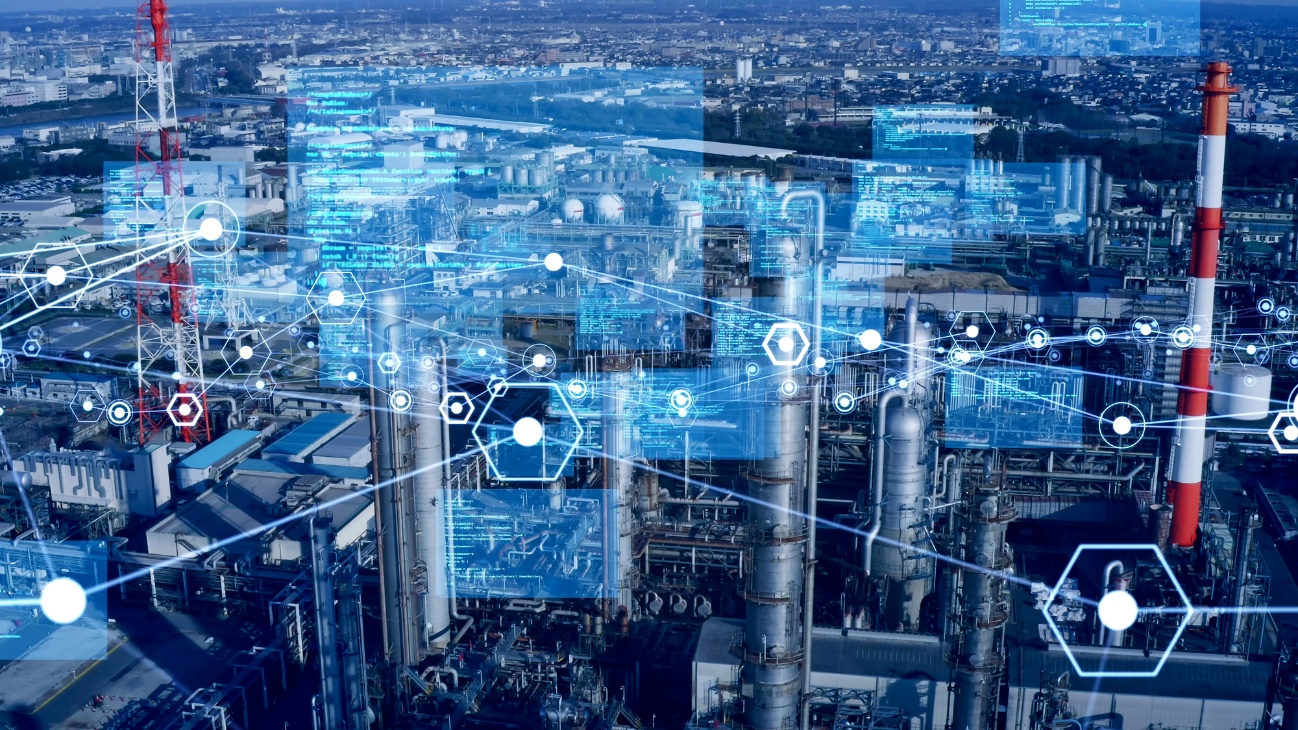
中小・零細製造業のデジタル化【基幹システム導入_ベンダー検討前編】
2021.07.16
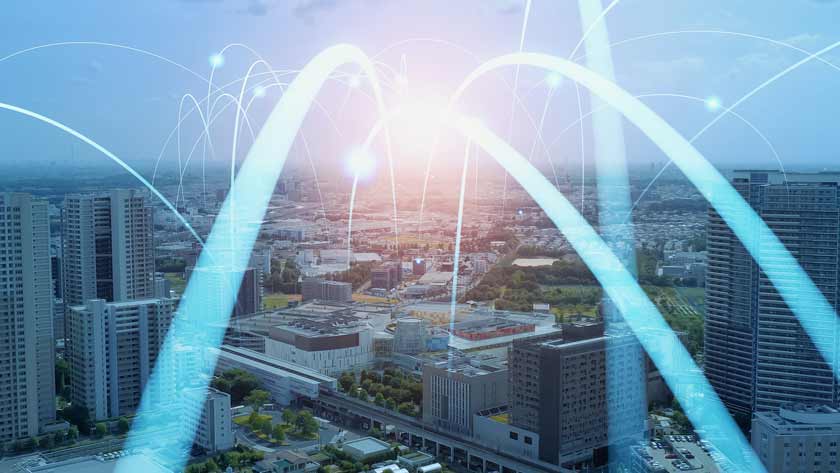
DXで生産性を向上させている製造業の特徴
2022.02.15