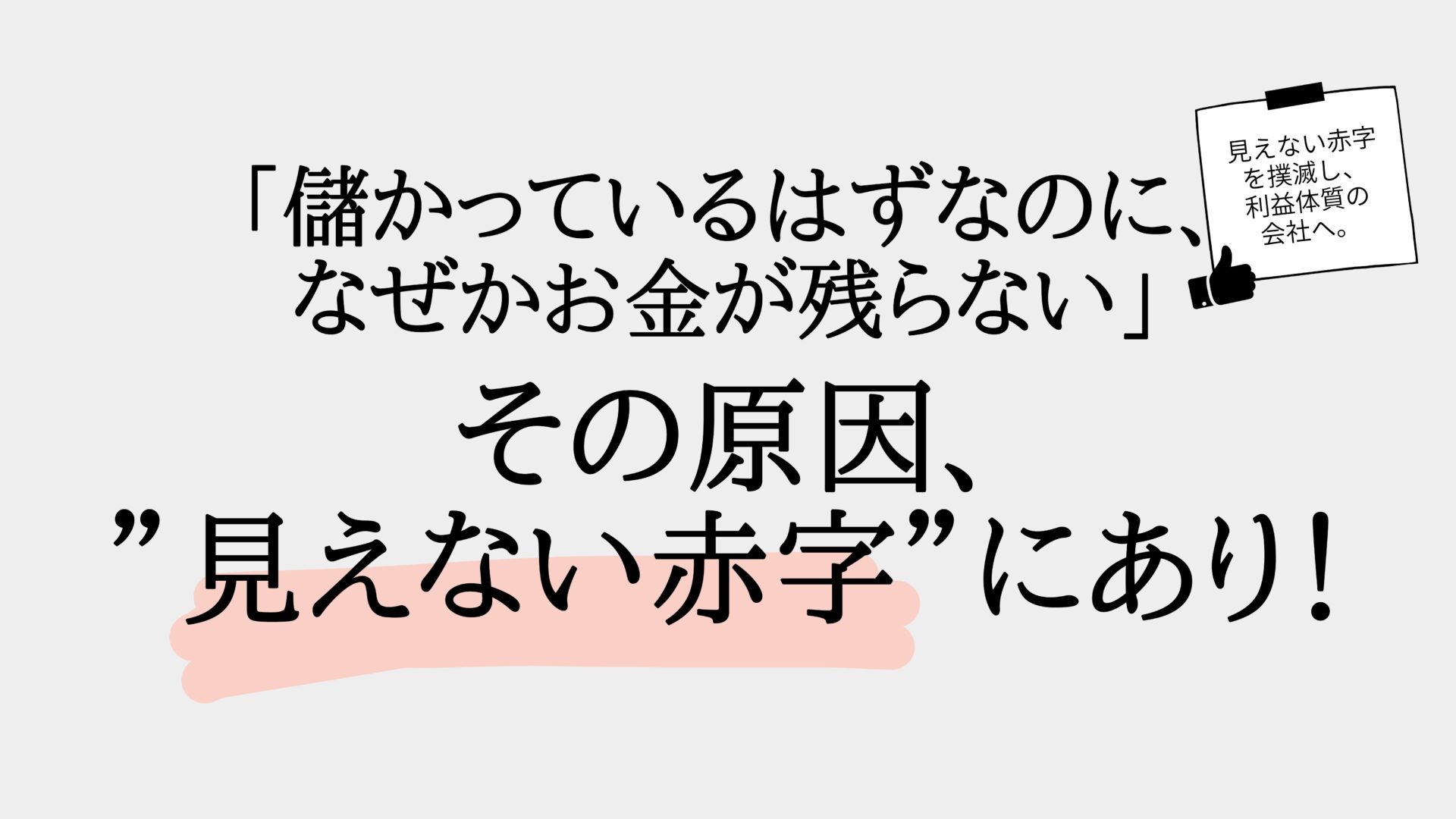
「儲かっているはずなのに、なぜかお金が残らない」その原因、”見えない赤字”にあり!
2025.07.16
月末の試算表を見て、首をかしげる。
「売上は立っている。忙しく工場も稼働している。なのに、なぜか手元にお金が残らない…」。
機械加工業の経営者であれば、一度はこのような経験があるのではないでしょうか。その、漠然とした不安の正体。それは、あなたの会社に潜む「見えない赤字」かもしれません。
特に、以下のような状況に心当たりはありませんか?
見積りは、長年使っている価格表や、担当者の「勘」に頼っている。
「あの客先は、大体このくらいの金額」という経験則で見積りを出している。
どの製品が儲かっていて、どの製品が赤字なのか、正確には把握できていない。
これらはすべて、危険な「どんぶり勘定」のサインです。そして、このどんぶり勘定が、見積りと実際の利益が大きく異なる最大の原因、すなわち”見えない赤字”を生み出しているのです。
見積原価と実際原価のズレが利益を蝕む
見積り段階での甘い原価計算は、静かに、しかし確実に会社の利益を蝕んでいきます。例えば、ある製品の見積りを工数10時間と想定して提出したとしましょう。しかし、実際に製作してみると、段取りに手間取ったり、予期せぬトラブルが発生したりして、15時間かかってしまった。この5時間分のズレは、そのまま会社の損失となります。
このような「見積原価」と「実際原価」のギャップが、一つ、また一つと積み重なることで、「儲かっているはずなのに、なぜかお金が残らない」という事態を招くのです。ひどい場合には、赤字が常態化し、会社の存続すら危うくします。
脱・どんぶり勘定!3日で始める「現場主導の原価管理」
「原価管理の重要性は分かっている。でも、高額な生産管理システムを導入する余裕はないし、何から手をつけていいか分からない…」。
そうしたお悩みは、非常によく分かります。しかし、ご安心ください。精緻な原価管理は、高価なシステムがなければ始められないわけではありません。
重要なのは、まず原価の「予実管理」を徹底すること。つまり、「見積原価」と「実際原価」のズレを正確に把握し、その原因を追求する仕組みを作ることです。そして、その仕組みは、驚くほどシンプルに、そして低コストで構築することが可能です。
実は、現場で働くスタッフ一人ひとりが、マシンST(設備時間)やマンST(作業時間)を意識し、記録するだけで、原価の「見える化」は大きく前進します。高額なシステムは不要です。使い慣れたExcelやスプレッドシートを活用し、3日もあれば、現場主導の予実原価管理をスタートさせることができます。
【機械加工業向け 利益を生む戦略的値付け経営セミナー】では、まさにこの「3日で始められる、現場主導の原価管理方法」を具体的にお伝えします。チャージレート(時間当たりコスト)の正しい設定方法から、現場に負担をかけずに工数を集計する仕組みづくりまで、すぐに実践できるノウハウを公開。曖昧な原価計算と決別し、作る前後の原価ギャップを最小化して、確実に利益を確保する具体策を学んでみませんか。
「見えない赤字」を撲滅し、利益体質の会社へ。
「どんぶり勘定」から脱却し、すべての仕事で適正な利益を確保する。その第一歩は、正確な原価把握から始まります。もう「なぜかお金が残らない」と悩むのは終わりにしましょう。
▼セミナー詳細・お申し込みはこちら
https://www.funaisoken.co.jp/seminar/130813
機械加工業向け 利益を生む戦略的値付け経営セミナー
値下げ圧力に屈しない!勘に頼らない!
「簡易ITツール」による原価管理と、粗利を死守する「攻めの値決め」で、利益体質になる方法 月末の試算表を見て、首をかしげる。
「売上は立っている。忙しく工場も稼働している。なのに、なぜか手元にお金が残らない…」。
機械加工業の経営者であれば、一度はこのような経験があるのではないでしょうか。その、漠然とした不安の正体。それは、あなたの会社に潜む「見えない赤字」かもしれません。
特に、以下のような状況に心当たりはありませんか?
見積りは、長年使っている価格表や、担当者の「勘」に頼っている。
「あの客先は、大体このくらいの金額」という経験則で見積りを出している。
どの製品が儲かっていて、どの製品が赤字なのか、正確には把握できていない。
これらはすべて、危険な「どんぶり勘定」のサインです。そして、このどんぶり勘定が、見積りと実際の利益が大きく異なる最大の原因、すなわち”見えない赤字”を生み出しているのです。
見積原価と実際原価のズレが利益を蝕む
見積り段階での甘い原価計算は、静かに、しかし確実に会社の利益を蝕んでいきます。例えば、ある製品の見積りを工数10時間と想定して提出したとしましょう。しかし、実際に製作してみると、段取りに手間取ったり、予期せぬトラブルが発生したりして、15時間かかってしまった。この5時間分のズレは、そのまま会社の損失となります。
このような「見積原価」と「実際原価」のギャップが、一つ、また一つと積み重なることで、「儲かっているはずなのに、なぜかお金が残らない」という事態を招くのです。ひどい場合には、赤字が常態化し、会社の存続すら危うくします。
脱・どんぶり勘定!3日で始める「現場主導の原価管理」
「原価管理の重要性は分かっている。でも、高額な生産管理システムを導入する余裕はないし、何から手をつけていいか分からない…」。
そうしたお悩みは、非常によく分かります。しかし、ご安心ください。精緻な原価管理は、高価なシステムがなければ始められないわけではありません。
重要なのは、まず原価の「予実管理」を徹底すること。つまり、「見積原価」と「実際原価」のズレを正確に把握し、その原因を追求する仕組みを作ることです。そして、その仕組みは、驚くほどシンプルに、そして低コストで構築することが可能です。
実は、現場で働くスタッフ一人ひとりが、マシンST(設備時間)やマンST(作業時間)を意識し、記録するだけで、原価の「見える化」は大きく前進します。高額なシステムは不要です。使い慣れたExcelやスプレッドシートを活用し、3日もあれば、現場主導の予実原価管理をスタートさせることができます。
【機械加工業向け 利益を生む戦略的値付け経営セミナー】では、まさにこの「3日で始められる、現場主導の原価管理方法」を具体的にお伝えします。チャージレート(時間当たりコスト)の正しい設定方法から、現場に負担をかけずに工数を集計する仕組みづくりまで、すぐに実践できるノウハウを公開。曖昧な原価計算と決別し、作る前後の原価ギャップを最小化して、確実に利益を確保する具体策を学んでみませんか。
「見えない赤字」を撲滅し、利益体質の会社へ。
「どんぶり勘定」から脱却し、すべての仕事で適正な利益を確保する。その第一歩は、正確な原価把握から始まります。もう「なぜかお金が残らない」と悩むのは終わりにしましょう。
▼セミナー詳細・お申し込みはこちら
https://www.funaisoken.co.jp/seminar/130813
機械加工業向け 利益を生む戦略的値付け経営セミナー
値下げ圧力に屈しない!勘に頼らない!
「簡易ITツール」による原価管理と、粗利を死守する「攻めの値決め」で、利益体質になる方法