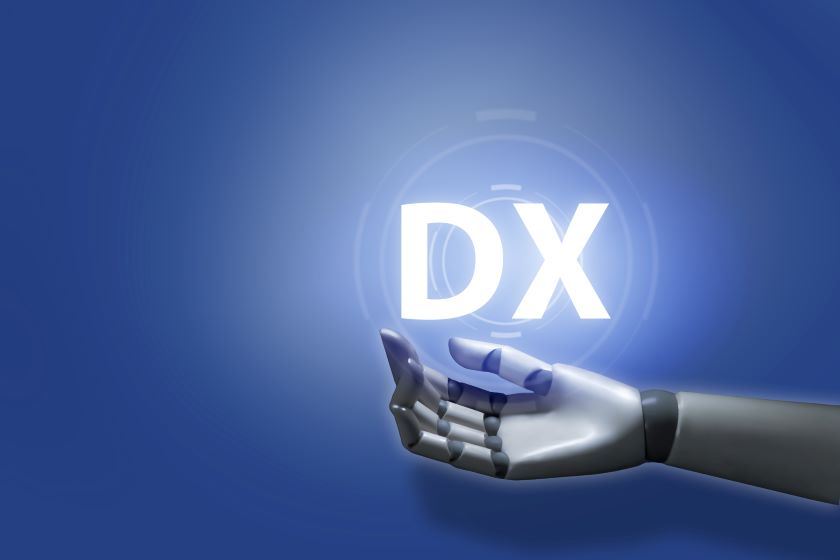
改定ものづくり補助金 省力化(オーダーメイド)枠を説明&活用案を紹介
2024.01.11
既に多くの注目を集めている「第17次ものづくり補助金(正式名称「ものづくり・商業・サービス補助金」)のなかでも、特に注目されているのが「省力化(オーダーメイド)枠」です。本コラムでは「省力化(オーダーメイド)枠」について紹介しています。
「省力化(オーダーメイド)枠」の要件はまだすべて公開されてはいません。今わかっている情報で、補助金申請書にどのようなポイントを盛り込む必要があるのかを解説させていただきます。また、どのような活用案が考えられるのか、仮説を含みますが、いくつか記載してみましたので、是非、一読していただき、自社の事業計画の参考にしていただければ幸いです。また、不明点や質問などがあれば、お気軽に私たちにご連絡ください。貴社の事業背景をお聞きした上で、アドバイスをさせていただきます。
1.省力化(オーダーメイド)枠について
(1)補助対象経費
補助対象経費の項目については、以下に様に記載されています。
「機械装置・システム構築費(必須)、技術導入費、専門家経費、運搬費、クラウドサービス利用費、原材料費、外注費、知的財産権等関連経費」
機械装置・システム構築費は必須と併記されていることから、この費目は必須です
(2)補助上限額・補助率について
補助率は、中小企業で1/2以内、小規模・再生事業者は2/3以内
補助上限額は、従業員数によって異なります。
・従業員数5人以下 750万円
・従業員数6~20人 1,500万円
・従業員数21~50人 3,000万円
・従業員数51~99人 5,000万円
・従業員数100人以上 8,000万円
上記に加えて、「大幅賃上げに係る補助額上限引き上げの特例」を行う場合、補助上限額を250万円~2,000万円を上乗せされます。
・従業員数5人以下 1,000万円
・従業員数6~20人 2,000万円
・従業員数21~50人 4,000万円
・従業員数51~99人 6,500万円
・従業員数100人以上 1億円
「大幅賃上げに係る補助額上限引き上げの特例」の要件:
補助業終了後、3~5年で大幅な賃上げに取り組む事業者は以下の要件を満たす必要があります。また、賃上げに係る計画書を提出することが必須です。
1)付加価値額 年平均成長率+3%以上(基本要件と同じ)
2)給与支給総額 年平均成長率+6%以上(基本要件と異なる)
3)最低賃金 事業場内最低賃金を地域別最低賃金+50円以上の水準にしたうえで、毎年、事業場内最低を+50円以上増額(基本要件と異なる)
【参考】基本要件
1)付加価値額 年平均成長率+3%以上
2)給与支給総額 年平均成長率+1.5%以上増加
3)最低賃金 地域別最低賃金+30円以上の水準とする
(3)要件未達の場合の補助金返還義務について
基本要件等が未達の場合、補助金返還義務があります。こちらもよく認識しておく必要があります。
詳細はもの補助事務局から追って公表される予定です。
1)基本要件が未達の場合
・事業計画終了時点において、基本要件2)給与支給総額が未達の場合、補助金の一部を返還
・事業計画期間中の毎年3月末時点において基本要件3)が未達の場合、補助金の一部を返還
2)大幅な賃上げに係る補助上限額引き上げの特例(以下、賃上げ特例)の要件が未達の場合
・事業計画終了時点において、賃上げ特例の要件2)給与支給総額が未達の場合、補助金上乗せ分を返還
・事業計画期間中の毎年3月末時点において賃上げ特例の要件3)が未達の場合、補助金上乗せ分を返還
(4)対象事業・活用イメージについて
対象事業の要件は以下のように定められています。
人手不足の解消に向けて、デジタル技術※1 等を活用した専用設備(オーダーメイド設備)※2 の導入等により、革新的な生産プロセス・サービス提供方法の効率化・高度化を図る取り組みに必要な設備・システム投資等を支援※3
※1:デジタル技術とは AI 、ロボット、センサー等をいう。
※2:ロボット単体の導入ではなく、外部のシステムインテグレータ( Sier )との連携などによりロボットシステム等を構築したものをいう。
※3:基本要件に加えた追加要件あり(詳細は追ってもの補助事務局から公表予定)
活用イメージの例として、下記が挙げられています。
熟練技術者が手作業で行っていた組立工程に、システムインテグレータ(SIer)と共同で開発した AI や画像判別技術を用いた自動組立ロボットを導入し、完全自動化・ 24 時間操業を実現。組立工程における生産性が向上するとともに、熟練技術者は付加価値の高い業務に従事することが可能となった。
以上の情報から、下記のポイントが計画に盛り込まれている必要があることが読み取れます。
・技術的な課題に対する、革新的な開発が必要
・自社に合わせた開発かつ外部業者との協力が必要
・省人化ではなく、省力化であること
・既存業務の置き換えではなく、改善効果(生産性向上、生産量増加⇒売上増加)があること
補助金を申請する際には、上記のポイントと審査項目をわかりすく記載した事業計画書を提出する必要があります。私たちにご連絡いただければ、貴社の業務・設備投資計画を詳細にお聞きして、申請要件を満たすようにストーリー作りを支援させていただきます。
2.独自の活用イメージについて
以下にもの補助金 省力化(オーダーメイド)枠の筆者独自の活用イメージをあげさせていただきます。
(1)精密加工を行っている伝統的な手動切削加工工程に、切削加工機メーカーと共同開発した最新5軸マシニングセンターとロボットアームを導入。材料搬出入の自動化および複数軸の連続自動加工が可能になったことで、生産効率の大幅向上と品質安定化を達成。従来の作業者は、より価格単価の高い試作品の製造に従事することが可能となった。
(2)自社のプラスチック射出成型ラインは生産効率と計画柔軟性に問題があったため、SIerと共同で開発した高性能3Dプリンターとリアルタイム監視システム、自動搬送ラインを複数導入することで、複雑な形状の部品も迅速に生産可能になり、生産効率の向上と24時間操業を可能にした。一人の作業者で複数台を担当することが可能になり、作業者ひとり当たりの付加価値額も増加した。
(3)金属の曲げ・溶接加工の属人化解消と生産量増加を目的に、ロボットアームと自動材料搬送システム、3D画像検査システム、生産管理システムを導入。24時間の生産対応と品質安定化、安全性向上が実現した。生産管理システムで進捗状況が見えることから、従来の作業者は、新たな顧客ニーズに対応するために加工技術開発に従事することが可能となった。
以上のように今後、この補助金を活用し、大胆な設備投資に取り組むことで自社の競争力強化を実現することが可能です。今回の募集枠では、間に合わない可能性もありますが、今後、補助金事業が継続していくことは見込めますので、今から検討をして来年、再来年の準備をしておくことは、大変重要で必要なことです。
3.まとめ
2024年度ものづくり補助金の省力化(オーダーメイド)枠について説明させていただきました。他の枠として、製品・サービス高付加価値枠(通常類型・成長分野進出類型(DX/GX))、グローバル枠がありますのでそちらも必要に応じて確認していただければと思います。
2024年度ものづくり補助金を活用して、省力化のための設備投資や、製品・サービス高付加価値化やDX,GX、海外事業の拡大を行う予定があれば、補助事業の実績報告が2024年12月10日であるということを念頭に、発注・納品等のスケジュールを組んでいただく必要があるでしょう。
本コラムを読んでいただき、質問・不明点・相談したいことなどあればお気軽にご連絡ください。また、補助金活用に関して支援が必要な場合もご相談ください。
私どもは、企業の中に入り込み、企業に寄り添い、計画を立案実行し定着・継続的な改善まで支援させて頂き、経営指標を改善することがゴールですので、最後まで伴走させていただきます。
最後までお読みいただきありがとうございました。
ものづくり補助金最新動向レポート
▼事例レポート無料ダウンロードお申し込みはこちら▼
ものづくり補助金(正式名称:「ものづくり・商業・サービス補助金」)の活用を検討している経営者様、次回申請の準備をしている経営者様にまず読んでいただきたいレポートです。
2023年12月に中小企業庁から次回以降のものづくり補助金の要件情報が一部公開されました。その内容からものつくり補助金に変更があることが明らかになりました。このレポートでは新たな要件を公開情報を基に整理しています。
ものづくり補助金の仕様を考えている経営者様は必ず押さえておくべき内容を記載したレポートです。
https://www.funaisoken.co.jp/dl-contents/smart-factory__02292_S045
■関連するセミナーのご案内
■東京&大阪 2拠点にて開催!!
【目指すは投資回収3年!協働ロボット活用事例特集!社長セミナー】
~中小製造業で40台以上の協働ロボットの稼働に成功した社長から学ぶ!
セミナー詳細・申込はこちらから
https://www.funaisoken.co.jp/seminar/105866
協働ロボットの活用事例特集!
中小製造業の皆様、このセミナーを見逃すわけにはいきません!
ロボット活用成功事例がここに集結します!
低コストでの導入方法、自動化生産の具体的な手法、人手不足を解消する秘策、生産性を引き上げるノウハウ...全てがここで明かされます!
船井総合研究所と愛同工業の著名な社長が登壇し、現場目線からの貴重な情報を提供します!
東京会場・大阪会場での開催となります!
このセミナーが御社の製造現場を変えるきっかけになるかもしれません!
空きは限られていますので、今すぐウェブサイトからお申し込みください。
協働ロボットの力を最大限に引き出し、成果を最短3年で得るチャンスです!
■開催日程
以下の日程よりご都合の良い日程をお選び下さい
※内容は全て一緒です
東京会場 2024/01/23 (火) 13:00~16:00
大阪会場 2024/01/29 (月) 13:00~16:00
お申し込みはこちらから⇒
https://www.funaisoken.co.jp/seminar/107400 いつも当コラムをご愛読いただきありがとうございます。
既に多くの注目を集めている「第17次ものづくり補助金(正式名称「ものづくり・商業・サービス補助金」)のなかでも、特に注目されているのが「省力化(オーダーメイド)枠」です。本コラムでは「省力化(オーダーメイド)枠」について紹介しています。
「省力化(オーダーメイド)枠」の要件はまだすべて公開されてはいません。今わかっている情報で、補助金申請書にどのようなポイントを盛り込む必要があるのかを解説させていただきます。また、どのような活用案が考えられるのか、仮説を含みますが、いくつか記載してみましたので、是非、一読していただき、自社の事業計画の参考にしていただければ幸いです。また、不明点や質問などがあれば、お気軽に私たちにご連絡ください。貴社の事業背景をお聞きした上で、アドバイスをさせていただきます。
1.省力化(オーダーメイド)枠について
(1)補助対象経費
補助対象経費の項目については、以下に様に記載されています。
「機械装置・システム構築費(必須)、技術導入費、専門家経費、運搬費、クラウドサービス利用費、原材料費、外注費、知的財産権等関連経費」
機械装置・システム構築費は必須と併記されていることから、この費目は必須です
(2)補助上限額・補助率について
補助率は、中小企業で1/2以内、小規模・再生事業者は2/3以内
補助上限額は、従業員数によって異なります。
・従業員数5人以下 750万円
・従業員数6~20人 1,500万円
・従業員数21~50人 3,000万円
・従業員数51~99人 5,000万円
・従業員数100人以上 8,000万円
上記に加えて、「大幅賃上げに係る補助額上限引き上げの特例」を行う場合、補助上限額を250万円~2,000万円を上乗せされます。
・従業員数5人以下 1,000万円
・従業員数6~20人 2,000万円
・従業員数21~50人 4,000万円
・従業員数51~99人 6,500万円
・従業員数100人以上 1億円
「大幅賃上げに係る補助額上限引き上げの特例」の要件:
補助業終了後、3~5年で大幅な賃上げに取り組む事業者は以下の要件を満たす必要があります。また、賃上げに係る計画書を提出することが必須です。
1)付加価値額 年平均成長率+3%以上(基本要件と同じ)
2)給与支給総額 年平均成長率+6%以上(基本要件と異なる)
3)最低賃金 事業場内最低賃金を地域別最低賃金+50円以上の水準にしたうえで、毎年、事業場内最低を+50円以上増額(基本要件と異なる)
【参考】基本要件
1)付加価値額 年平均成長率+3%以上
2)給与支給総額 年平均成長率+1.5%以上増加
3)最低賃金 地域別最低賃金+30円以上の水準とする
(3)要件未達の場合の補助金返還義務について
基本要件等が未達の場合、補助金返還義務があります。こちらもよく認識しておく必要があります。
詳細はもの補助事務局から追って公表される予定です。
1)基本要件が未達の場合
・事業計画終了時点において、基本要件2)給与支給総額が未達の場合、補助金の一部を返還
・事業計画期間中の毎年3月末時点において基本要件3)が未達の場合、補助金の一部を返還
2)大幅な賃上げに係る補助上限額引き上げの特例(以下、賃上げ特例)の要件が未達の場合
・事業計画終了時点において、賃上げ特例の要件2)給与支給総額が未達の場合、補助金上乗せ分を返還
・事業計画期間中の毎年3月末時点において賃上げ特例の要件3)が未達の場合、補助金上乗せ分を返還
(4)対象事業・活用イメージについて
対象事業の要件は以下のように定められています。
人手不足の解消に向けて、デジタル技術※1 等を活用した専用設備(オーダーメイド設備)※2 の導入等により、革新的な生産プロセス・サービス提供方法の効率化・高度化を図る取り組みに必要な設備・システム投資等を支援※3
※1:デジタル技術とは AI 、ロボット、センサー等をいう。
※2:ロボット単体の導入ではなく、外部のシステムインテグレータ( Sier )との連携などによりロボットシステム等を構築したものをいう。
※3:基本要件に加えた追加要件あり(詳細は追ってもの補助事務局から公表予定)
活用イメージの例として、下記が挙げられています。
熟練技術者が手作業で行っていた組立工程に、システムインテグレータ(SIer)と共同で開発した AI や画像判別技術を用いた自動組立ロボットを導入し、完全自動化・ 24 時間操業を実現。組立工程における生産性が向上するとともに、熟練技術者は付加価値の高い業務に従事することが可能となった。
以上の情報から、下記のポイントが計画に盛り込まれている必要があることが読み取れます。
・技術的な課題に対する、革新的な開発が必要
・自社に合わせた開発かつ外部業者との協力が必要
・省人化ではなく、省力化であること
・既存業務の置き換えではなく、改善効果(生産性向上、生産量増加⇒売上増加)があること
補助金を申請する際には、上記のポイントと審査項目をわかりすく記載した事業計画書を提出する必要があります。私たちにご連絡いただければ、貴社の業務・設備投資計画を詳細にお聞きして、申請要件を満たすようにストーリー作りを支援させていただきます。
2.独自の活用イメージについて
以下にもの補助金 省力化(オーダーメイド)枠の筆者独自の活用イメージをあげさせていただきます。
(1)精密加工を行っている伝統的な手動切削加工工程に、切削加工機メーカーと共同開発した最新5軸マシニングセンターとロボットアームを導入。材料搬出入の自動化および複数軸の連続自動加工が可能になったことで、生産効率の大幅向上と品質安定化を達成。従来の作業者は、より価格単価の高い試作品の製造に従事することが可能となった。
(2)自社のプラスチック射出成型ラインは生産効率と計画柔軟性に問題があったため、SIerと共同で開発した高性能3Dプリンターとリアルタイム監視システム、自動搬送ラインを複数導入することで、複雑な形状の部品も迅速に生産可能になり、生産効率の向上と24時間操業を可能にした。一人の作業者で複数台を担当することが可能になり、作業者ひとり当たりの付加価値額も増加した。
(3)金属の曲げ・溶接加工の属人化解消と生産量増加を目的に、ロボットアームと自動材料搬送システム、3D画像検査システム、生産管理システムを導入。24時間の生産対応と品質安定化、安全性向上が実現した。生産管理システムで進捗状況が見えることから、従来の作業者は、新たな顧客ニーズに対応するために加工技術開発に従事することが可能となった。
以上のように今後、この補助金を活用し、大胆な設備投資に取り組むことで自社の競争力強化を実現することが可能です。今回の募集枠では、間に合わない可能性もありますが、今後、補助金事業が継続していくことは見込めますので、今から検討をして来年、再来年の準備をしておくことは、大変重要で必要なことです。
3.まとめ
2024年度ものづくり補助金の省力化(オーダーメイド)枠について説明させていただきました。他の枠として、製品・サービス高付加価値枠(通常類型・成長分野進出類型(DX/GX))、グローバル枠がありますのでそちらも必要に応じて確認していただければと思います。
2024年度ものづくり補助金を活用して、省力化のための設備投資や、製品・サービス高付加価値化やDX,GX、海外事業の拡大を行う予定があれば、補助事業の実績報告が2024年12月10日であるということを念頭に、発注・納品等のスケジュールを組んでいただく必要があるでしょう。
本コラムを読んでいただき、質問・不明点・相談したいことなどあればお気軽にご連絡ください。また、補助金活用に関して支援が必要な場合もご相談ください。
私どもは、企業の中に入り込み、企業に寄り添い、計画を立案実行し定着・継続的な改善まで支援させて頂き、経営指標を改善することがゴールですので、最後まで伴走させていただきます。
最後までお読みいただきありがとうございました。
ものづくり補助金最新動向レポート
▼事例レポート無料ダウンロードお申し込みはこちら▼
ものづくり補助金(正式名称:「ものづくり・商業・サービス補助金」)の活用を検討している経営者様、次回申請の準備をしている経営者様にまず読んでいただきたいレポートです。
2023年12月に中小企業庁から次回以降のものづくり補助金の要件情報が一部公開されました。その内容からものつくり補助金に変更があることが明らかになりました。このレポートでは新たな要件を公開情報を基に整理しています。
ものづくり補助金の仕様を考えている経営者様は必ず押さえておくべき内容を記載したレポートです。
https://www.funaisoken.co.jp/dl-contents/smart-factory__02292_S045
■関連するセミナーのご案内
■東京&大阪 2拠点にて開催!!
【目指すは投資回収3年!協働ロボット活用事例特集!社長セミナー】
~中小製造業で40台以上の協働ロボットの稼働に成功した社長から学ぶ!
セミナー詳細・申込はこちらから
https://www.funaisoken.co.jp/seminar/105866
協働ロボットの活用事例特集!
中小製造業の皆様、このセミナーを見逃すわけにはいきません!
ロボット活用成功事例がここに集結します!
低コストでの導入方法、自動化生産の具体的な手法、人手不足を解消する秘策、生産性を引き上げるノウハウ...全てがここで明かされます!
船井総合研究所と愛同工業の著名な社長が登壇し、現場目線からの貴重な情報を提供します!
東京会場・大阪会場での開催となります!
このセミナーが御社の製造現場を変えるきっかけになるかもしれません!
空きは限られていますので、今すぐウェブサイトからお申し込みください。
協働ロボットの力を最大限に引き出し、成果を最短3年で得るチャンスです!
■開催日程
以下の日程よりご都合の良い日程をお選び下さい
※内容は全て一緒です
東京会場 2024/01/23 (火) 13:00~16:00
大阪会場 2024/01/29 (月) 13:00~16:00
お申し込みはこちらから⇒
https://www.funaisoken.co.jp/seminar/107400