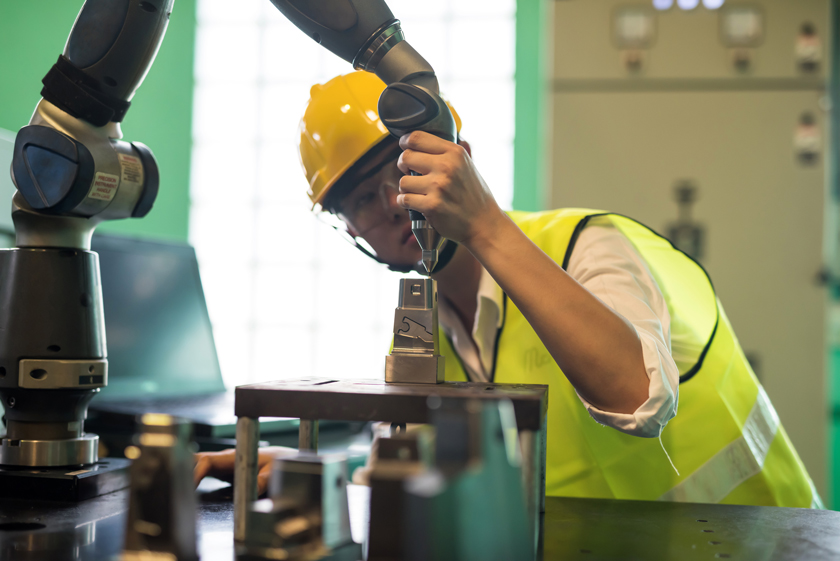
誰でも簡単に使えるロボット!!【協働ロボット】を活用して製造現場のDX化を推進
2022.03.31
1.協働ロボットとは何か
協働ロボットとは、人と一緒に作業を行う事の出来る産業用ロボットです。
本来産業用ロボットというのは、非常に力持ちです。ロボットの種類や大きさによるものの
人を遥かに超える大きな力をもっている為に産業用ロボットの稼働範囲に人が入ってしまうと重篤な災害を引き起こすリスクがあります。
その為、産業用ロボットの周囲には安全柵の設置が必要であり、安全柵はロボットが停止していないと開かない様になっています。
完全にロボットのみで完結するシステムであれば問題無いのですが、あくまで人が組立作業を行うが人の作業をロボットで補助して欲しいというニーズや、普段は必要無いが生産ラインに欠員等の人員不足等があった際にロボットを使用したい、というニーズが多くあります。
2013年12月に以下のとおり規制が緩和されたことをきっかけに、労働者に危険が生じない産業用ロボットの開発が進みました。それこそが協働ロボットです。
事業者は、産業用ロボットを運転する場合(教示等のために産業用ロボットを運転する場合及び産業用ロボットの運転中に次条に規定する作業を行わなければならない場合において産業用ロボットを運転するときを除く。)において、当該産業用ロボットに接触することにより労働者に危険が生ずるおそれのあるときは、さく又は囲いを設ける等当該危険を防止するために必要な措置を講じなければならない。
厚生労働省『安衛則第150条の4(運転中の危険の防止)』より
産業用ロボットを使用する事業者が、労働安全衛生法第28条の2による危険性等の調査(以下 「リスクアセスメント」という。)に基づく措置を実施し、産業用ロボットに接触することにより労働者に危険の生ずるおそれが無くなったと評価できるときは、本条の「労働者に危険が生ずるおそれのあるとき」に該当しません。
『安衛則第150条の4(運転中の危険の防止)』(平成25年12月24日付基発1224第2号通達)より
協働ロボットは一般的にモーターの定格出力が80Wを超えない様になっています。そして何かに衝突したり大きな負荷がロボットに掛かった場合は即時モータ電源が遮断されるようになっています。
感覚的に言えば、道を歩いていてすれ違う人と軽く肩がぶつかった時の衝撃よりも軽い衝撃でロボットは停止する様になっており、作業者が仮にロボットに接触しても大きな災害につながるリスクは小さいのです。
2.協働ロボットの特徴
協働ロボットは安全の為に他の産業用ロボットに比べて非常に非力に作られています。
非力であるが故に大きなモノや重たいモノは持つ事も素早く動く事も出来ません。
しかし、下記の様な特長を持っています。
非常にコンパクトで軽量な為に必要に応じてロボットを移動して別の場所で使う事が出来る。
※協働ロボットの架台にキャスターが付いているモノも多いです。
直接教示が可能なモノが多く簡単に動かす事が出来る。※直接教示はダイレクトティーチングとも呼ばれ、人の手でロボットハンドを指定したい場所に動かしてポイントを登録するだけでティーチング出来るという教示法。簡単で早い教示が可能です。
コンセント繋げれば使える。大がかりなシステムが必要無い為、導入コストを引き下げる事が出来る。
※協働ロボット単体の単価は一般の産業用ロボットに比べて高めですが、安全対策機器に掛かる費用やシステム設計費等を抑制する事が出来るのでシステム全体としての費用は抑える事が出来ます。
ビジョンセンサ等をセンシング機器とアッセンブリで販売されているモノも多く用途に合わせて選ぶ事が出来る。
操作が簡単に誰でも出来る様にアプリケーションの開発が進んでおり、一般的な産業用ロボットに比べて遥かに使いやすい。
協働ロボットはこのような特徴をもっており、一般の産業用ロボットでは不可能な事が可能となる面をもっています。作業者のすぐそばで作業をする為に、安全性と操作性に非常に特化されており【身近なロボット】として生産現場で活躍しています。
協働ロボットは非常に非力と記述しましたが、現在の開発競争の中、可搬重量が数10KGを超える協働ロボットも出てきています。安全対策の進歩により、かなり力のある協働ロボットも世に出てきており、数年後には協働ロボットは一般産業用ロボットの可搬性能に並んでいくかも知れませんね。
3. 協働ロボットの主要メーカと商品
現在下記の様なロボットメーカーが協働ロボットを開発し販売しています。
ユニバーサルロボット(デンマーク) 「URシリーズ」
安川電機(日本) 「MOTOMAN-HC」
ファナック(日本) 「CRシリーズ」
ABB (スイス) 「YuMi®」
KUKA (ドイツ) 「LBR iiwa」
川崎重工(日本) 「duAro」
三菱電機(日本) 「MELFA ASSISTA」
住友重機械工業(日本) 「Sawyer」
デンソーウェーブ(日本) 「COBOTTA」
オムロン(日本) 「TMシリーズ」
不二越(日本) 「CZ10」
TechMan Robot(台湾) 「TMシリーズ」
Doosan Robotics(韓国) 「Mシリーズ」
KAWADA Robotics (日本) 「NEXTAGE」
ここに記載したメーカーと商品はごく一部になります。
国内海外問わず様々なメーカーが協働ロボット市場に参入しており、これまでにない協働ロボットがどんどん世に送り出されています。
世界シェアでいえばユニバーサルロボットが圧倒的なシェアを誇っていると言えますが、各社様々な特徴を持った協働ロボットをリリースしており一概にどこのロボットが一番良いと言う事は出来ません。
協働ロボットの価格については、韓国や台湾の協働ロボットは価格面において非常に優位性があります。
一般的に協働ロボットは500~600万円程するモノですが、300万円台で購入できるモノも出ています。今後更に性能の良いものがより安価に購入できる様になってくると思います。
日本においては双椀ロボットの開発も進んでおり、ロボットアームが2本ありビジョンセンサも標準装備されている事で対応可能な加工や工程が幅広く非常に汎用性に富んでいます。本来複数軸のロボットの制御やティーチングは非常に難しいのですが、これを簡単に安全に出来るようにアプリケーションを工夫しており非常に使い勝手が良いです。
4.協働ロボットの活用方法や導入事例
協働ロボットは様々な工程での活用が可能です。下記の様な工程はもちろんの事、アイデア次第では更に活用範囲は広がる事でしょう。
ピック・アンド・プレイス・・部品運搬に活用
射出成形・・射出成型機からのワークの取り出しに活用
CNC・・工作機械からのワークの着脱に活用
梱包およびパレタイジング・・・自動積み付けに活用
品質検査・・・カメラによる自動良否判定に活用
組み立て・・小物精密部品の自動組み立て
研磨・・・自動でのバフ研磨やバリ取りにも活用
ねじ止め・・・自動でのねじ止めやねじ供給に活用
接着、溶接作業・・・シーリング等の接着剤塗布作業から溶接作業にも活用
様々な工程で導入されている協働ロボットですが、やはり導入企業に共通している活用方法は、1台のロボットを色々な場所に移動して多用途に活用しているという点です。
例えば、
欠員が出た生産工程に協働ロボットを持って生産を行う。
作業負荷の高い製品の生産を行う時だけ使う。
生産タクトに遅れが出ているボトルネックの工程に持っていき人員の作業の補助をさせる等です。
各社各々補助的なモノとしていろいろな活用方法を各社アイデアと工夫で取り組んでいます。
使い方次第では人が行っていた工程に協働ロボットを導入した結果生産性が何倍にもする事も普通にあり、生産現場の頼れるパートナーとなっています。
これまで協働ロボットについて、記述してきましたが如何でしたか?
自動化は進めていきたいが、需要が不透明で大がかりな専用機の導入が難しいと考えていらっしゃる方も多いと思いますが、大がかりな専用自動機では無く、色々な工程で人間の作業を補助するロボットをいれて全体の生産性を高めていくという自動化もあります。
現在協働ロボット市場は活発に開発競争が行われており、平行して現場への活用も進んできています。
世界的に見ても欧州や中国を中心に製造現場に協働ロボットが数十台並んでいる工場も珍しくありません。一度協働ロボットの導入を検討してみてはいかがでしょうか。
■最短半年でロボット導入を成功させる方法
▼事例レポート無料ダウンロードお申し込みはこちら▼
https://www.funaisoken.co.jp/dl-contents/smart-factory_smart-factory_00145
目次
ロボット導入が失敗する3つの理由
初めてのロボットはこれを使え!!
具体的活用事例
本レポートでは、ロボット導入が失敗する理由とその解決策、さらに、具体的な活用事例をご紹介しています。
食品・飲料品メーカー経営者セミナー「DX経営戦略!」
多品種小ロット&労働集約型生産における自動化・ロボット化&デジタル化・AI化・IoT化!
↓↓お申し込みはこちらから↓↓
https://smart-factory.funaisoken.co.jp/event/
講座内容
第一講座 食品・飲料品メーカーDX取組事例講座編 「全国各地で見られる食品・飲料品メーカーでの自動化・ロボット化&デジタル化・AI化・IoT化取組事例」
多品種小ロット&労働集約型の食品・飲料品メーカーが取り組んでいるDX化事例
人海戦術に依存している食品・飲料品メーカーが生産現場で取り組んでいる自動化・ロボット化事例
生産技術・生産計画・生産管理でDXを活用して熟練者依存からの脱却に取り組んでいる食品・飲料品メーカーの事例
属人的な生産現場でデジタル化・AI化・IoT化に取り組んでいる食品・飲料品メーカーの事例
経営者として経営管理全般でDX化に邁進している食品・飲料品メーカーの事例
第二講座 食品・飲料品メーカーDX戦略講座編 「食品・飲料品メーカー経営者が取り組むべきDX戦略」
食品・飲料品メーカーの経営にDXを活用する方法
”経営者”が知っておくべき自動化・ロボット化&デジタル化・AI化・IoT化の具体的な活用とは?
漠然とした理論・概論ではなく、現場で即使えて実践的なDX導入手順
全日程オンラインでの開催となります
2022/05/12 (木) 13:00~15:00
2022/05/17 (火) 13:00~15:00
2022/05/19 (木) 13:00~15:00
無料お申し込みはこちら
このセミナーは終了しました。最新のセミナーはこちらから。
https://smart-factory.funaisoken.co.jp/event/ 1.協働ロボットとは何か
協働ロボットとは、人と一緒に作業を行う事の出来る産業用ロボットです。
本来産業用ロボットというのは、非常に力持ちです。ロボットの種類や大きさによるものの
人を遥かに超える大きな力をもっている為に産業用ロボットの稼働範囲に人が入ってしまうと重篤な災害を引き起こすリスクがあります。
その為、産業用ロボットの周囲には安全柵の設置が必要であり、安全柵はロボットが停止していないと開かない様になっています。
完全にロボットのみで完結するシステムであれば問題無いのですが、あくまで人が組立作業を行うが人の作業をロボットで補助して欲しいというニーズや、普段は必要無いが生産ラインに欠員等の人員不足等があった際にロボットを使用したい、というニーズが多くあります。
2013年12月に以下のとおり規制が緩和されたことをきっかけに、労働者に危険が生じない産業用ロボットの開発が進みました。それこそが協働ロボットです。
事業者は、産業用ロボットを運転する場合(教示等のために産業用ロボットを運転する場合及び産業用ロボットの運転中に次条に規定する作業を行わなければならない場合において産業用ロボットを運転するときを除く。)において、当該産業用ロボットに接触することにより労働者に危険が生ずるおそれのあるときは、さく又は囲いを設ける等当該危険を防止するために必要な措置を講じなければならない。
厚生労働省『安衛則第150条の4(運転中の危険の防止)』より
産業用ロボットを使用する事業者が、労働安全衛生法第28条の2による危険性等の調査(以下 「リスクアセスメント」という。)に基づく措置を実施し、産業用ロボットに接触することにより労働者に危険の生ずるおそれが無くなったと評価できるときは、本条の「労働者に危険が生ずるおそれのあるとき」に該当しません。
『安衛則第150条の4(運転中の危険の防止)』(平成25年12月24日付基発1224第2号通達)より
協働ロボットは一般的にモーターの定格出力が80Wを超えない様になっています。そして何かに衝突したり大きな負荷がロボットに掛かった場合は即時モータ電源が遮断されるようになっています。
感覚的に言えば、道を歩いていてすれ違う人と軽く肩がぶつかった時の衝撃よりも軽い衝撃でロボットは停止する様になっており、作業者が仮にロボットに接触しても大きな災害につながるリスクは小さいのです。
2.協働ロボットの特徴
協働ロボットは安全の為に他の産業用ロボットに比べて非常に非力に作られています。
非力であるが故に大きなモノや重たいモノは持つ事も素早く動く事も出来ません。
しかし、下記の様な特長を持っています。
非常にコンパクトで軽量な為に必要に応じてロボットを移動して別の場所で使う事が出来る。
※協働ロボットの架台にキャスターが付いているモノも多いです。
直接教示が可能なモノが多く簡単に動かす事が出来る。※直接教示はダイレクトティーチングとも呼ばれ、人の手でロボットハンドを指定したい場所に動かしてポイントを登録するだけでティーチング出来るという教示法。簡単で早い教示が可能です。
コンセント繋げれば使える。大がかりなシステムが必要無い為、導入コストを引き下げる事が出来る。
※協働ロボット単体の単価は一般の産業用ロボットに比べて高めですが、安全対策機器に掛かる費用やシステム設計費等を抑制する事が出来るのでシステム全体としての費用は抑える事が出来ます。
ビジョンセンサ等をセンシング機器とアッセンブリで販売されているモノも多く用途に合わせて選ぶ事が出来る。
操作が簡単に誰でも出来る様にアプリケーションの開発が進んでおり、一般的な産業用ロボットに比べて遥かに使いやすい。
協働ロボットはこのような特徴をもっており、一般の産業用ロボットでは不可能な事が可能となる面をもっています。作業者のすぐそばで作業をする為に、安全性と操作性に非常に特化されており【身近なロボット】として生産現場で活躍しています。
協働ロボットは非常に非力と記述しましたが、現在の開発競争の中、可搬重量が数10KGを超える協働ロボットも出てきています。安全対策の進歩により、かなり力のある協働ロボットも世に出てきており、数年後には協働ロボットは一般産業用ロボットの可搬性能に並んでいくかも知れませんね。
3. 協働ロボットの主要メーカと商品
現在下記の様なロボットメーカーが協働ロボットを開発し販売しています。
ユニバーサルロボット(デンマーク) 「URシリーズ」
安川電機(日本) 「MOTOMAN-HC」
ファナック(日本) 「CRシリーズ」
ABB (スイス) 「YuMi®」
KUKA (ドイツ) 「LBR iiwa」
川崎重工(日本) 「duAro」
三菱電機(日本) 「MELFA ASSISTA」
住友重機械工業(日本) 「Sawyer」
デンソーウェーブ(日本) 「COBOTTA」
オムロン(日本) 「TMシリーズ」
不二越(日本) 「CZ10」
TechMan Robot(台湾) 「TMシリーズ」
Doosan Robotics(韓国) 「Mシリーズ」
KAWADA Robotics (日本) 「NEXTAGE」
ここに記載したメーカーと商品はごく一部になります。
国内海外問わず様々なメーカーが協働ロボット市場に参入しており、これまでにない協働ロボットがどんどん世に送り出されています。
世界シェアでいえばユニバーサルロボットが圧倒的なシェアを誇っていると言えますが、各社様々な特徴を持った協働ロボットをリリースしており一概にどこのロボットが一番良いと言う事は出来ません。
協働ロボットの価格については、韓国や台湾の協働ロボットは価格面において非常に優位性があります。
一般的に協働ロボットは500~600万円程するモノですが、300万円台で購入できるモノも出ています。今後更に性能の良いものがより安価に購入できる様になってくると思います。
日本においては双椀ロボットの開発も進んでおり、ロボットアームが2本ありビジョンセンサも標準装備されている事で対応可能な加工や工程が幅広く非常に汎用性に富んでいます。本来複数軸のロボットの制御やティーチングは非常に難しいのですが、これを簡単に安全に出来るようにアプリケーションを工夫しており非常に使い勝手が良いです。
4.協働ロボットの活用方法や導入事例
協働ロボットは様々な工程での活用が可能です。下記の様な工程はもちろんの事、アイデア次第では更に活用範囲は広がる事でしょう。
ピック・アンド・プレイス・・部品運搬に活用
射出成形・・射出成型機からのワークの取り出しに活用
CNC・・工作機械からのワークの着脱に活用
梱包およびパレタイジング・・・自動積み付けに活用
品質検査・・・カメラによる自動良否判定に活用
組み立て・・小物精密部品の自動組み立て
研磨・・・自動でのバフ研磨やバリ取りにも活用
ねじ止め・・・自動でのねじ止めやねじ供給に活用
接着、溶接作業・・・シーリング等の接着剤塗布作業から溶接作業にも活用
様々な工程で導入されている協働ロボットですが、やはり導入企業に共通している活用方法は、1台のロボットを色々な場所に移動して多用途に活用しているという点です。
例えば、
欠員が出た生産工程に協働ロボットを持って生産を行う。
作業負荷の高い製品の生産を行う時だけ使う。
生産タクトに遅れが出ているボトルネックの工程に持っていき人員の作業の補助をさせる等です。
各社各々補助的なモノとしていろいろな活用方法を各社アイデアと工夫で取り組んでいます。
使い方次第では人が行っていた工程に協働ロボットを導入した結果生産性が何倍にもする事も普通にあり、生産現場の頼れるパートナーとなっています。
これまで協働ロボットについて、記述してきましたが如何でしたか?
自動化は進めていきたいが、需要が不透明で大がかりな専用機の導入が難しいと考えていらっしゃる方も多いと思いますが、大がかりな専用自動機では無く、色々な工程で人間の作業を補助するロボットをいれて全体の生産性を高めていくという自動化もあります。
現在協働ロボット市場は活発に開発競争が行われており、平行して現場への活用も進んできています。
世界的に見ても欧州や中国を中心に製造現場に協働ロボットが数十台並んでいる工場も珍しくありません。一度協働ロボットの導入を検討してみてはいかがでしょうか。
■最短半年でロボット導入を成功させる方法
▼事例レポート無料ダウンロードお申し込みはこちら▼
https://www.funaisoken.co.jp/dl-contents/smart-factory_smart-factory_00145
目次
ロボット導入が失敗する3つの理由
初めてのロボットはこれを使え!!
具体的活用事例
本レポートでは、ロボット導入が失敗する理由とその解決策、さらに、具体的な活用事例をご紹介しています。
食品・飲料品メーカー経営者セミナー「DX経営戦略!」
多品種小ロット&労働集約型生産における自動化・ロボット化&デジタル化・AI化・IoT化!
↓↓お申し込みはこちらから↓↓
https://smart-factory.funaisoken.co.jp/event/
講座内容
第一講座 食品・飲料品メーカーDX取組事例講座編 「全国各地で見られる食品・飲料品メーカーでの自動化・ロボット化&デジタル化・AI化・IoT化取組事例」
多品種小ロット&労働集約型の食品・飲料品メーカーが取り組んでいるDX化事例
人海戦術に依存している食品・飲料品メーカーが生産現場で取り組んでいる自動化・ロボット化事例
生産技術・生産計画・生産管理でDXを活用して熟練者依存からの脱却に取り組んでいる食品・飲料品メーカーの事例
属人的な生産現場でデジタル化・AI化・IoT化に取り組んでいる食品・飲料品メーカーの事例
経営者として経営管理全般でDX化に邁進している食品・飲料品メーカーの事例
第二講座 食品・飲料品メーカーDX戦略講座編 「食品・飲料品メーカー経営者が取り組むべきDX戦略」
食品・飲料品メーカーの経営にDXを活用する方法
”経営者”が知っておくべき自動化・ロボット化&デジタル化・AI化・IoT化の具体的な活用とは?
漠然とした理論・概論ではなく、現場で即使えて実践的なDX導入手順
全日程オンラインでの開催となります
2022/05/12 (木) 13:00~15:00
2022/05/17 (火) 13:00~15:00
2022/05/19 (木) 13:00~15:00
無料お申し込みはこちら
このセミナーは終了しました。最新のセミナーはこちらから。
https://smart-factory.funaisoken.co.jp/event/