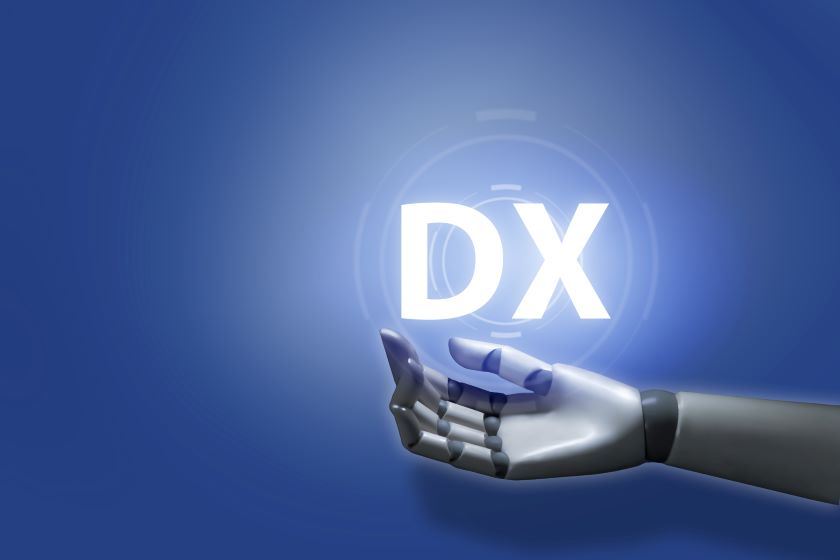
製造業における構内物流の自動化
2024.01.23
1.ロボット産業の成長と需要の拡大
2022年の日本では、ロボットの生産・出荷台数が過去最高となり、出荷総額も1兆円を超えました。
これまでの電気・半導体・自動車産業だけでなく、幅広い産業にてロボットが使用されるようになっています。
特に近年の人件費高騰や人手不足を背景としてロボットの需要が高まり、協働ロボットの使いやすさなど活用領域の裾野は広がりをみせています。
これまでの大企業を中心としたロボットの導入が中小企業でも導入しやすい環境となっており、ロボットの活用を通じて生産性を向上する取り組みが求められています。
2.労働力不足への対策としてのロボット活用
2030年には労働需要に対して供給人口が10%不足すると試算されています。
労働力不足はそれぞれの企業が直面する課題となります。
対策としては、働く女性を増やす、働くシニア人材を増やす、働く外国人を増やすという、労働力の確保を推進することのほか、生産性を上げて、少ない人材でこれまで以上の成果を出す仕組みへ転換をしていくことが重要です。
設備導入による業務の自動化が生産性を上げる一つの手段として注目されています。
3.工場内の生産工程のムダ削減の重要性
工場内の生産工程においては、部材の探索や運搬、作業の待ち時間など、ムダな作業が存在します。
これらのムダを削減することで、作業者はより付加価値の高い業務に移行することができます。
また、労働人口の減少も企業にとって深刻な課題であり、工場内の生産工程のムダ削減は労働人口不足への対策としても重要です。
4.自動化技術の活用
工場内の生産工程のムダ削減には、無人搬送機やロボットなどの自動化技術が活用されています。
例えば、配膳ロボットの導入により、作業者の負担が軽減され、作業時間が削減されました。
また、物流倉庫ではピッキングや搬送作業を自動化するためにロボットが導入され、人員削減や労働時間の短縮が実現されました。
さらに、部品のハンドリングや重量検査作業もロボットによって自動化され、労働生産性の向上と品質の安定化が図られました。
自動化技術の活用により、工場内の生産工程のムダ削減と労働人口不足への対策が同時に実現されます。
5.設備導入フローと保全活動の重要性
自動化技術の導入には、設備導入フローと保全活動が重要です。
設備の選定やレイアウトの見直し、生産シミュレーションの活用など、効果的な設備導入フローを構築することが必要です。
また、定期保全によって稼働率の向上や品質の維持、安全の確保などが実現されます。
設備導入フローと保全活動の取り組みにより、自動化技術の効果を最大限に引き出すことができます。
6.まとめと展望
工場内物流の自動化は、生産工程のムダ削減や労働人口不足への対策において重要な要素です。
無人搬送機やロボットなどの自動化技術の活用により、作業者はより付加価値の高い業務に注力することができます。
また、設備導入フローと保全活動の取り組みも重要であり、定期保全によって効率的な生産が実現されます。
工場内物流の自動化は、労働力不足への対策としても有効であり、生産性の向上や省人化、高品質などの効果が期待できます。
ロボット産業の成長と労働力不足への対策としてのロボット活用の重要性を説明しました。
実際に導入する際においては、設備の選定や保全活動、生産性向上のための継続的な取り組みが必要です。
しかしながら、今後もさらなる技術の進化や補助金の活用など、ロボットや設備を導入しやすい環境が整ってきています。
ロボットの活用により、労働力不足に対する課題を解決し、企業の生産性向上や競争力強化に貢献することが期待されます。
船井総研では、個別固有のご相談に対してオンライン相談を提供しており、具体的な対策の一歩を踏み出すお手伝いをしています。
■関連するセミナーのご案内
従業員50~500名製造業 工場内物流・工程間搬送の自動化
AGV・AMR・自動搬送システム・パレタイズロボット・ハンドリングロボットの活用
セミナー詳細・申込はこちらから
https://www.funaisoken.co.jp/seminar/108174
■開催日程
全てオンライン開催となります
以下の日程よりご都合の良い日程をお選び下さい
※内容は全て一緒です
2024/02/13 (火) 13:00~15:00
2024/02/15 (木) 13:00~15:00
2024/02/19 (月) 13:00~15:00
お申し込みはこちらから⇒
https://www.funaisoken.co.jp/seminar/108174
中堅・中小製造業の経営者向け 工場物流の自動化事例解説レポート
▼事例レポート無料ダウンロードお申し込みはこちら▼
「こうなりたい!」と思っている経営者様におすすめ
工場内の物流を自動化して生産性を向上したいと思っている経営者様
工場内の物流を自動化して省人化したいと思っている経営者様
工場内物流の自動化成功事例を知りたいと思っている経営者様
工場内物流の自動化を進めるための具体的な方法を知りたいと思っている経営者様
https://www.funaisoken.co.jp/dl-contents/smart-factory_smart-factory_02125_S045 いつも当コラムをご愛読いただきありがとうございます。
1.ロボット産業の成長と需要の拡大
2022年の日本では、ロボットの生産・出荷台数が過去最高となり、出荷総額も1兆円を超えました。
これまでの電気・半導体・自動車産業だけでなく、幅広い産業にてロボットが使用されるようになっています。
特に近年の人件費高騰や人手不足を背景としてロボットの需要が高まり、協働ロボットの使いやすさなど活用領域の裾野は広がりをみせています。
これまでの大企業を中心としたロボットの導入が中小企業でも導入しやすい環境となっており、ロボットの活用を通じて生産性を向上する取り組みが求められています。
2.労働力不足への対策としてのロボット活用
2030年には労働需要に対して供給人口が10%不足すると試算されています。
労働力不足はそれぞれの企業が直面する課題となります。
対策としては、働く女性を増やす、働くシニア人材を増やす、働く外国人を増やすという、労働力の確保を推進することのほか、生産性を上げて、少ない人材でこれまで以上の成果を出す仕組みへ転換をしていくことが重要です。
設備導入による業務の自動化が生産性を上げる一つの手段として注目されています。
3.工場内の生産工程のムダ削減の重要性
工場内の生産工程においては、部材の探索や運搬、作業の待ち時間など、ムダな作業が存在します。
これらのムダを削減することで、作業者はより付加価値の高い業務に移行することができます。
また、労働人口の減少も企業にとって深刻な課題であり、工場内の生産工程のムダ削減は労働人口不足への対策としても重要です。
4.自動化技術の活用
工場内の生産工程のムダ削減には、無人搬送機やロボットなどの自動化技術が活用されています。
例えば、配膳ロボットの導入により、作業者の負担が軽減され、作業時間が削減されました。
また、物流倉庫ではピッキングや搬送作業を自動化するためにロボットが導入され、人員削減や労働時間の短縮が実現されました。
さらに、部品のハンドリングや重量検査作業もロボットによって自動化され、労働生産性の向上と品質の安定化が図られました。
自動化技術の活用により、工場内の生産工程のムダ削減と労働人口不足への対策が同時に実現されます。
5.設備導入フローと保全活動の重要性
自動化技術の導入には、設備導入フローと保全活動が重要です。
設備の選定やレイアウトの見直し、生産シミュレーションの活用など、効果的な設備導入フローを構築することが必要です。
また、定期保全によって稼働率の向上や品質の維持、安全の確保などが実現されます。
設備導入フローと保全活動の取り組みにより、自動化技術の効果を最大限に引き出すことができます。
6.まとめと展望
工場内物流の自動化は、生産工程のムダ削減や労働人口不足への対策において重要な要素です。
無人搬送機やロボットなどの自動化技術の活用により、作業者はより付加価値の高い業務に注力することができます。
また、設備導入フローと保全活動の取り組みも重要であり、定期保全によって効率的な生産が実現されます。
工場内物流の自動化は、労働力不足への対策としても有効であり、生産性の向上や省人化、高品質などの効果が期待できます。
ロボット産業の成長と労働力不足への対策としてのロボット活用の重要性を説明しました。
実際に導入する際においては、設備の選定や保全活動、生産性向上のための継続的な取り組みが必要です。
しかしながら、今後もさらなる技術の進化や補助金の活用など、ロボットや設備を導入しやすい環境が整ってきています。
ロボットの活用により、労働力不足に対する課題を解決し、企業の生産性向上や競争力強化に貢献することが期待されます。
船井総研では、個別固有のご相談に対してオンライン相談を提供しており、具体的な対策の一歩を踏み出すお手伝いをしています。
■関連するセミナーのご案内
従業員50~500名製造業 工場内物流・工程間搬送の自動化
AGV・AMR・自動搬送システム・パレタイズロボット・ハンドリングロボットの活用
セミナー詳細・申込はこちらから
https://www.funaisoken.co.jp/seminar/108174
■開催日程
全てオンライン開催となります
以下の日程よりご都合の良い日程をお選び下さい
※内容は全て一緒です
2024/02/13 (火) 13:00~15:00
2024/02/15 (木) 13:00~15:00
2024/02/19 (月) 13:00~15:00
お申し込みはこちらから⇒
https://www.funaisoken.co.jp/seminar/108174
中堅・中小製造業の経営者向け 工場物流の自動化事例解説レポート
▼事例レポート無料ダウンロードお申し込みはこちら▼
「こうなりたい!」と思っている経営者様におすすめ
工場内の物流を自動化して生産性を向上したいと思っている経営者様
工場内の物流を自動化して省人化したいと思っている経営者様
工場内物流の自動化成功事例を知りたいと思っている経営者様
工場内物流の自動化を進めるための具体的な方法を知りたいと思っている経営者様
https://www.funaisoken.co.jp/dl-contents/smart-factory_smart-factory_02125_S045