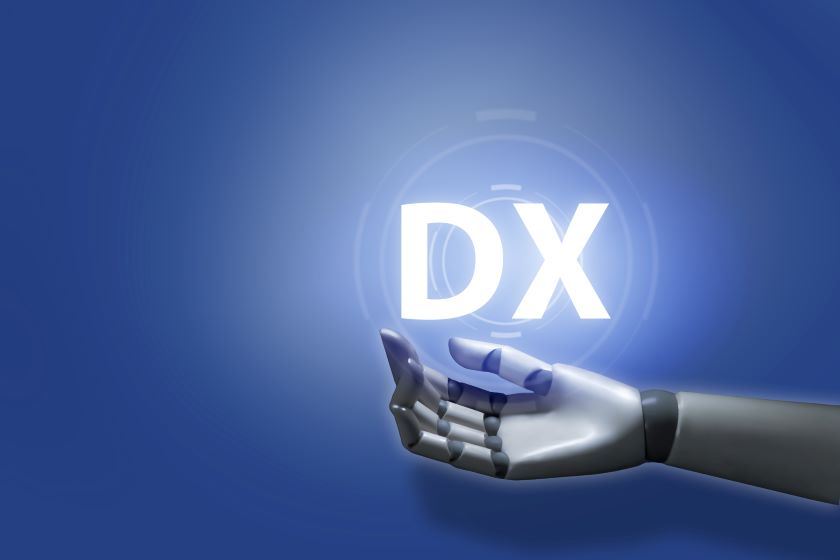
業務効率化とデジタル化を実現するためのシステム導入の課題と成功のポイント
2023.10.17
いつも当コラムをご愛読いただきありがとうございます
「業務効率化」、「脱属人化」、「デジタル化」の実現について、システム導入は有効的な方法の1つと言えます。
しかしシステムを導入するだけではこれらの目的に繋がらないと言えます。
また導入プロセスにおいて誤った方向へ進んでしまうと、属人化や非効率化を生み出してしまうという逆方向の可能性もあります。
そこで今回はシステム導入における課題と成功のポイントを幾つかお伝えいたします。
ご存知のとおり、製造原価には直間分類がございます。厳密な個別原価計算をするには、間接費を個々の製品に配賦する必要がございますが、一足飛びには難しく、またそこまで厳密に計算されている会社様は多くはありません。第一ステップは直接費の把握です。
そこで今回は、改めて製造原価について触れていきたいと思います。
1.システム導入で実現させるポイントを明確にする
システム導入の際に、まずは現状業務のヒアリングを行い、その作業をシステムで行うといった導入ケースはよく見られます。
しかしここの入り口をきっちり整理しないと、失敗の原因を生み出してしまいます。
それは現状業務をヒアリングしてもらえるということは、「現状業務は新システムでも採用される」という誤解が各個人の頭の中にインプットされる可能性があるからです。
もちろん組織の一部の主要メンバーは、システムに合わせて効率化、脱属人化を達成するという目的を認識した上でプロジェクトを進める意識がありますが、現場全てのメンバーには浸透しづらいものです。
解決策としては、例えばシステム導入設計時に、そのシステムの標準的機能に現状業務を合わせていくことを挙げたとすると、まずはその前提を全体で宣言することが重要です。
実際の導入シーンでよくあるケースとして、関係事務局内だけで、目的の共有を行ってしまい、現場の前提と認識の擦り合わせがされていなく、システム導入の後半になって、認識相違で振り戻しが発生したり、追加要件定義やカスタマイズ開発など、どんどん初期の構想と離れていってしまい、費用や期間が増大するといったことがあります。
このサイクルに入ってしまうと、進めれば進めるほど、深みにはまってしまう恐れがあり、軌道修正が難しくなります。
そうならないように常に前提目的を念頭に置いたうえで、全ての議論を始め、現場含めた関係者全員の意識を統一させることが重要と考えられます。
既存にとらわれずに業務を進める方法を現場一丸となって検討できるような議論を進めていけばシステム導入は必ず成功します。
2.システムのマニュアルは、操作用ではなく、運用マニュアルとする
前項で、既存に振り回されずにシステム導入を進めていくことをお伝えしましたが、次に重要なのはそのマニュアル化です。
導入時におけるマニュアルとしては、システム操作マニュアルが何百ページもあり、どこを読んでいいのか分からないので、独自で進めていたり、先輩に習った方法で進めている、といったケースがあります。
また現場ではシステムの使い方に関して、ベテランAさんは「他部署間の伝達に有効なので、入力項目の1、2、3を入力している」が新人Bさんは「入力項目の1,2だけ入力している」という具体例です。
これでは業務が正しく回らなく、人のスキルや独自性に左右されてしまいます。
解決策として、入力する項目は、1,2なのか、1,2,3なのかきちんとマニュアルで決めて、誰でも同じアウトプットにすることが重要です。
入力者による個人差を無くして誰でも同じ結果を出せるよう業務マニュアルを作成し、徹底的に順守していくことが重要です。
せっかく業務標準化の為の新システムを導入しても、使い方で個人差を発生させてしまうと、システム内部の属人化が進んでしまいます。
常に基本の運用マニュアル通りのオペレーションを徹底させることが業務標準化の正しい実践と言えます。
3.分析資料においても、導入設計時に明確にする
前項までで、システム仕様を整理し、運用マニュアルに沿って行くという話をしましたが、最後に重要なのは分析資料からの戦略についてです。
例えば基幹システムを導入すると、売上集計等様々なデータ分析を行っていきます。
これについても導入時にしっかりと設計を行うことがとても重要です。
よく分析関係は導入後に検討というフェーズがありますが、システム実装後に、やはりあの項目も追加しないと集計できない、入力フローとしても何か所も変更しなくてはいけない等と手戻りが発生してしまい、せっかくここまで決めた内容が崩されてしまい、導入期間が余計にかかることや工数追加の要因にもなりかねません。
本来のシステム導入のゴールは導入ではなく、正しい活用にあると考えます。
次年度以降の戦略をたてるうえで重要な指標を得ることが必要で、そこを見据えながらシステム導入を進めていくととてもスムーズに進行します。
それは目的に沿った内容で、設計構築を行っていくので、全体の整合性が繋がっていくからです。
現場もそのような意識で議論を進めていくと自然と必要な項目を洗い出してくれます。
そこへの導き出しを担っていくことがシステム導入成功に繋げる重要な役割と考えます。
4.まとめ
今回のまとめでございますが、システム導入実現に向けて重要なポイントは、「システム導入の目的を明確にする」、「マニュアルは運用マニュアルとする」、「分析資料もシステム設計時に検討する」の3点となります。
第一印象としてはどうしても現場の同意を得るのが難しい内容ではと捉えられがちですが、本来のシステム導入の目的を達成するのに不可欠であると言えます。
当初は不安を抱くメンバーも結果的に導入後にスムーズにストレスなく回り始めるシステムフローを振り返ると、導入してよかったと思えるはずです。
なぜならば個人個人の今までの余分な業務が結果的に取り除かれているからです。
常にベテランスタッフにダブルチェックで行っていた業務が新人でも1人でこなせるのですから。
このように人員リソースの不安を出来るだけ取り去り、日々の業務を回し続けることが迅速で安定した「標準化」の実現に向けて不可欠な要素となってきます。
■関連するセミナーのご案内
「多品種少量生産板金加工業の為の原価改善!」 社長セミナー
セミナー詳細・申込はこちらから
https://www.funaisoken.co.jp/seminar/104283
■開催日程
全てオンライン開催となります
以下の日程よりご都合の良い日程をお選び下さい
※内容は全て一緒です
2023/11/06 (月) 13:00~15:00
2023/11/08 (水) 13:00~15:00
2023/11/16 (木) 13:00~15:00
お申し込みはこちらから⇒
https://www.funaisoken.co.jp/seminar/104283
製造業経営者向け“基幹システム再構築戦略”解説レポート
▼事例レポート無料ダウンロードお申し込みはこちら▼
多くの製造業は、全体としての原価・利益は見えているが、個別の実際原価は、属人化している業務で運用されている事で見えにくくなっています。製品別個別、取引先個別、工程別個別の実際原価を把握することで実際の利益が見えてきます。
見える化、DX化により、適切なアクションを取ることが重要です。
本レポートでは見える化とDX化のポイントを解説します!
https://www.funaisoken.co.jp/dl-contents/smart-factory__02003_S045 いつも当コラムをご愛読いただきありがとうございます
「業務効率化」、「脱属人化」、「デジタル化」の実現について、システム導入は有効的な方法の1つと言えます。
しかしシステムを導入するだけではこれらの目的に繋がらないと言えます。
また導入プロセスにおいて誤った方向へ進んでしまうと、属人化や非効率化を生み出してしまうという逆方向の可能性もあります。
そこで今回はシステム導入における課題と成功のポイントを幾つかお伝えいたします。
ご存知のとおり、製造原価には直間分類がございます。厳密な個別原価計算をするには、間接費を個々の製品に配賦する必要がございますが、一足飛びには難しく、またそこまで厳密に計算されている会社様は多くはありません。第一ステップは直接費の把握です。
そこで今回は、改めて製造原価について触れていきたいと思います。
1.システム導入で実現させるポイントを明確にする
システム導入の際に、まずは現状業務のヒアリングを行い、その作業をシステムで行うといった導入ケースはよく見られます。
しかしここの入り口をきっちり整理しないと、失敗の原因を生み出してしまいます。
それは現状業務をヒアリングしてもらえるということは、「現状業務は新システムでも採用される」という誤解が各個人の頭の中にインプットされる可能性があるからです。
もちろん組織の一部の主要メンバーは、システムに合わせて効率化、脱属人化を達成するという目的を認識した上でプロジェクトを進める意識がありますが、現場全てのメンバーには浸透しづらいものです。
解決策としては、例えばシステム導入設計時に、そのシステムの標準的機能に現状業務を合わせていくことを挙げたとすると、まずはその前提を全体で宣言することが重要です。
実際の導入シーンでよくあるケースとして、関係事務局内だけで、目的の共有を行ってしまい、現場の前提と認識の擦り合わせがされていなく、システム導入の後半になって、認識相違で振り戻しが発生したり、追加要件定義やカスタマイズ開発など、どんどん初期の構想と離れていってしまい、費用や期間が増大するといったことがあります。
このサイクルに入ってしまうと、進めれば進めるほど、深みにはまってしまう恐れがあり、軌道修正が難しくなります。
そうならないように常に前提目的を念頭に置いたうえで、全ての議論を始め、現場含めた関係者全員の意識を統一させることが重要と考えられます。
既存にとらわれずに業務を進める方法を現場一丸となって検討できるような議論を進めていけばシステム導入は必ず成功します。
2.システムのマニュアルは、操作用ではなく、運用マニュアルとする
前項で、既存に振り回されずにシステム導入を進めていくことをお伝えしましたが、次に重要なのはそのマニュアル化です。
導入時におけるマニュアルとしては、システム操作マニュアルが何百ページもあり、どこを読んでいいのか分からないので、独自で進めていたり、先輩に習った方法で進めている、といったケースがあります。
また現場ではシステムの使い方に関して、ベテランAさんは「他部署間の伝達に有効なので、入力項目の1、2、3を入力している」が新人Bさんは「入力項目の1,2だけ入力している」という具体例です。
これでは業務が正しく回らなく、人のスキルや独自性に左右されてしまいます。
解決策として、入力する項目は、1,2なのか、1,2,3なのかきちんとマニュアルで決めて、誰でも同じアウトプットにすることが重要です。
入力者による個人差を無くして誰でも同じ結果を出せるよう業務マニュアルを作成し、徹底的に順守していくことが重要です。
せっかく業務標準化の為の新システムを導入しても、使い方で個人差を発生させてしまうと、システム内部の属人化が進んでしまいます。
常に基本の運用マニュアル通りのオペレーションを徹底させることが業務標準化の正しい実践と言えます。
3.分析資料においても、導入設計時に明確にする
前項までで、システム仕様を整理し、運用マニュアルに沿って行くという話をしましたが、最後に重要なのは分析資料からの戦略についてです。
例えば基幹システムを導入すると、売上集計等様々なデータ分析を行っていきます。
これについても導入時にしっかりと設計を行うことがとても重要です。
よく分析関係は導入後に検討というフェーズがありますが、システム実装後に、やはりあの項目も追加しないと集計できない、入力フローとしても何か所も変更しなくてはいけない等と手戻りが発生してしまい、せっかくここまで決めた内容が崩されてしまい、導入期間が余計にかかることや工数追加の要因にもなりかねません。
本来のシステム導入のゴールは導入ではなく、正しい活用にあると考えます。
次年度以降の戦略をたてるうえで重要な指標を得ることが必要で、そこを見据えながらシステム導入を進めていくととてもスムーズに進行します。
それは目的に沿った内容で、設計構築を行っていくので、全体の整合性が繋がっていくからです。
現場もそのような意識で議論を進めていくと自然と必要な項目を洗い出してくれます。
そこへの導き出しを担っていくことがシステム導入成功に繋げる重要な役割と考えます。
4.まとめ
今回のまとめでございますが、システム導入実現に向けて重要なポイントは、「システム導入の目的を明確にする」、「マニュアルは運用マニュアルとする」、「分析資料もシステム設計時に検討する」の3点となります。
第一印象としてはどうしても現場の同意を得るのが難しい内容ではと捉えられがちですが、本来のシステム導入の目的を達成するのに不可欠であると言えます。
当初は不安を抱くメンバーも結果的に導入後にスムーズにストレスなく回り始めるシステムフローを振り返ると、導入してよかったと思えるはずです。
なぜならば個人個人の今までの余分な業務が結果的に取り除かれているからです。
常にベテランスタッフにダブルチェックで行っていた業務が新人でも1人でこなせるのですから。
このように人員リソースの不安を出来るだけ取り去り、日々の業務を回し続けることが迅速で安定した「標準化」の実現に向けて不可欠な要素となってきます。
■関連するセミナーのご案内
「多品種少量生産板金加工業の為の原価改善!」 社長セミナー
セミナー詳細・申込はこちらから
https://www.funaisoken.co.jp/seminar/104283
■開催日程
全てオンライン開催となります
以下の日程よりご都合の良い日程をお選び下さい
※内容は全て一緒です
2023/11/06 (月) 13:00~15:00
2023/11/08 (水) 13:00~15:00
2023/11/16 (木) 13:00~15:00
お申し込みはこちらから⇒
https://www.funaisoken.co.jp/seminar/104283
製造業経営者向け“基幹システム再構築戦略”解説レポート
▼事例レポート無料ダウンロードお申し込みはこちら▼
多くの製造業は、全体としての原価・利益は見えているが、個別の実際原価は、属人化している業務で運用されている事で見えにくくなっています。製品別個別、取引先個別、工程別個別の実際原価を把握することで実際の利益が見えてきます。
見える化、DX化により、適切なアクションを取ることが重要です。
本レポートでは見える化とDX化のポイントを解説します!
https://www.funaisoken.co.jp/dl-contents/smart-factory__02003_S045