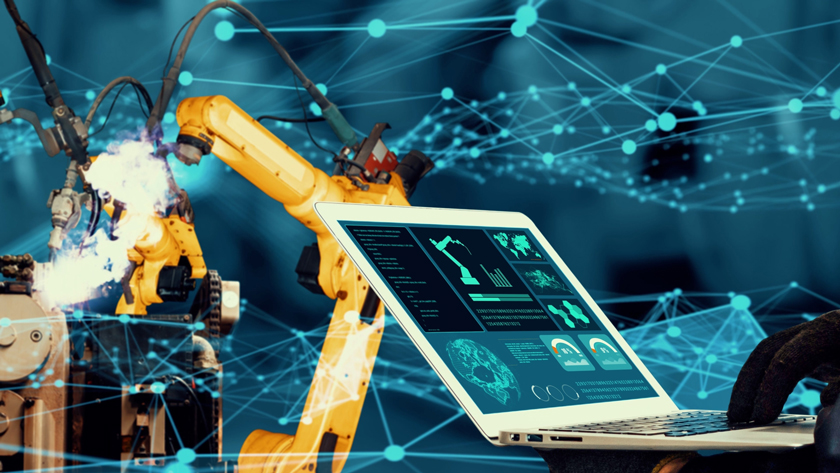
ロボットをフル活用!ティーチングレスを実現する方法
2022.07.08
▼無料ダウンロードはこちらをクリック
1.はじめに
昨今、日本でも急速にロボット導入が進み、大手・中堅企業はもちろんのこと中小製造業でもロボットが導入されていることが珍しくなくなりました。
しかしながら多くの企業に導入されているものの、実際活用できている企業はほんの一握りなのが現状です。活用できていない原因はいくつかありますが、主な原因の一つが「ティーチング」です。ロボットを動かすためにはロボットに動作を教え込む必要がありそのために必要な作業がティーチングになります。
ティーチング作業は非常に複雑、かつ専門知識を要する作業であり、専門のロボットプログラマーが行うのが一般的です。ロボットを動かすにはペンダント(操作パネル)を使います。
このペンダントでティーチングの修正や動作確認を行っていくのですが、一般的に使用されているペンダントの画面はプログラムが羅列された文字だらけの画面であり非常に複雑です。
また、例えば金属加工品において、全ての加工品が完全に同じ形状なことはまずありえません。ロボットは決められた動きを繰りかえす為、そういったワークごとのズレには対応できません。
上記のような課題により特に多品種少量生産の企業においてロボットを使いこなすのは至難の業といえるでしょう。ただ、近年ではこうした課題に対するソリューションが多く登場してきておりますので、本コラムではティーチングレスを実現させるための方法を紹介いたします。
2.オフラインティーチングソフト
オフラインティーチングとは、実機を用いずにPCの操作にてロボットティーチングを実践する方法です。
本来ペンダントと呼ばれるリモコンの様なモノで、手動によるロボットの移動とポイント登録を繰り返して加工動作一連のPRGを作成していきますが、オフラインティーチングソフトは3D-CADデータを基にPC上でロボットプログラムの作成が可能となります。様々なシュミレーションを安全な環境で生産現場のロボットを停止せずに行う事が出来ます。
高機能型のソフトウェアでは加工開始点と終了点を指定するだけで、自動で加工パスを生成してくれるソフトもあります。
更に干渉確認や特異点回避(ロボットがエラーを起こしやすい場所)の機能もあり、実機を動かさずにほとんどのティーチング作業を完了させる事が出来ます。
ただし、あくまでもCADモデル上でのシュミレーションになりますので、実機での調整は必須です。
8割程度はオフラインティーチングで作成し、作ったPRGを実機に書き込んだのちに、ペンダントで微調整していく事で大幅にティーチングに掛かる時間を削減する事が出来ます。
非常に便利なソフトウェアですが、上述したとおり3D-CADが必須です。
自社での3D設計→自社生産であればこのようなソフトは絶大な効果を発揮出来ますが、外部から受注している仕事の場合難易度が高いのは事実です。
中小製造業では、今も2Dや手書きの図面がFAXでやり取りされる事がまだまだ多く、受注段階で3D-CADを貰える事はあまり無いという実態があります。
本来であれば受注直後にCADモデルが客先から支給され、それをもとにオフラインティーチングを実施し、現場の微調整をかけてロボットで着工という流れでものづくりをしていければ良いですが、現状ではそういう環境になっていない場合も多く、自社で3Dモデルの作成が必須となります。
3.センサー活用
3Dのレーザーセンサーやレーザースキャナーを活用することで、現物合わせて位置補正を行うことができます。そのため、ワークごとの形状差や溶接によるひずみがあってもワークの変化に対して自動補正をかけることができます。都度都度ティーチングの修正を行う必要がないため、位置ズレやワークの加工誤差・形状の変化が大きいものをロボットで取り扱っている場合は特に力を発揮します。
センサーにも多くの種類が存在しており、接触式で安価なタッチセンサーから、3Dスキャナーと高性能なソフトウェアを使った補正システムまで、幅広く存在しています。
センサーによっては、2次元のものや3次元的に補正をかけられるセンサーがあったり、対象の工程(溶接やハンドリングなど)に合ったセンサーなど多種多様なものがあるので、どの工程のどのワークを対象にするのが投資対効果の良いかをよく分析したうえで、それに合ったセンサーを検討されるのが良いでしょう。
▼無料ダウンロードはこちらをクリック ▼無料ダウンロードはこちらをクリック
1.はじめに
昨今、日本でも急速にロボット導入が進み、大手・中堅企業はもちろんのこと中小製造業でもロボットが導入されていることが珍しくなくなりました。
しかしながら多くの企業に導入されているものの、実際活用できている企業はほんの一握りなのが現状です。活用できていない原因はいくつかありますが、主な原因の一つが「ティーチング」です。ロボットを動かすためにはロボットに動作を教え込む必要がありそのために必要な作業がティーチングになります。
ティーチング作業は非常に複雑、かつ専門知識を要する作業であり、専門のロボットプログラマーが行うのが一般的です。ロボットを動かすにはペンダント(操作パネル)を使います。
このペンダントでティーチングの修正や動作確認を行っていくのですが、一般的に使用されているペンダントの画面はプログラムが羅列された文字だらけの画面であり非常に複雑です。
また、例えば金属加工品において、全ての加工品が完全に同じ形状なことはまずありえません。ロボットは決められた動きを繰りかえす為、そういったワークごとのズレには対応できません。
上記のような課題により特に多品種少量生産の企業においてロボットを使いこなすのは至難の業といえるでしょう。ただ、近年ではこうした課題に対するソリューションが多く登場してきておりますので、本コラムではティーチングレスを実現させるための方法を紹介いたします。
2.オフラインティーチングソフト
オフラインティーチングとは、実機を用いずにPCの操作にてロボットティーチングを実践する方法です。
本来ペンダントと呼ばれるリモコンの様なモノで、手動によるロボットの移動とポイント登録を繰り返して加工動作一連のPRGを作成していきますが、オフラインティーチングソフトは3D-CADデータを基にPC上でロボットプログラムの作成が可能となります。様々なシュミレーションを安全な環境で生産現場のロボットを停止せずに行う事が出来ます。
高機能型のソフトウェアでは加工開始点と終了点を指定するだけで、自動で加工パスを生成してくれるソフトもあります。
更に干渉確認や特異点回避(ロボットがエラーを起こしやすい場所)の機能もあり、実機を動かさずにほとんどのティーチング作業を完了させる事が出来ます。
ただし、あくまでもCADモデル上でのシュミレーションになりますので、実機での調整は必須です。
8割程度はオフラインティーチングで作成し、作ったPRGを実機に書き込んだのちに、ペンダントで微調整していく事で大幅にティーチングに掛かる時間を削減する事が出来ます。
非常に便利なソフトウェアですが、上述したとおり3D-CADが必須です。
自社での3D設計→自社生産であればこのようなソフトは絶大な効果を発揮出来ますが、外部から受注している仕事の場合難易度が高いのは事実です。
中小製造業では、今も2Dや手書きの図面がFAXでやり取りされる事がまだまだ多く、受注段階で3D-CADを貰える事はあまり無いという実態があります。
本来であれば受注直後にCADモデルが客先から支給され、それをもとにオフラインティーチングを実施し、現場の微調整をかけてロボットで着工という流れでものづくりをしていければ良いですが、現状ではそういう環境になっていない場合も多く、自社で3Dモデルの作成が必須となります。
3.センサー活用
3Dのレーザーセンサーやレーザースキャナーを活用することで、現物合わせて位置補正を行うことができます。そのため、ワークごとの形状差や溶接によるひずみがあってもワークの変化に対して自動補正をかけることができます。都度都度ティーチングの修正を行う必要がないため、位置ズレやワークの加工誤差・形状の変化が大きいものをロボットで取り扱っている場合は特に力を発揮します。
センサーにも多くの種類が存在しており、接触式で安価なタッチセンサーから、3Dスキャナーと高性能なソフトウェアを使った補正システムまで、幅広く存在しています。
センサーによっては、2次元のものや3次元的に補正をかけられるセンサーがあったり、対象の工程(溶接やハンドリングなど)に合ったセンサーなど多種多様なものがあるので、どの工程のどのワークを対象にするのが投資対効果の良いかをよく分析したうえで、それに合ったセンサーを検討されるのが良いでしょう。
▼無料ダウンロードはこちらをクリック